Sampling and shearing method for steel for pressure vessel
A pressure vessel and shear stress technology, applied in the direction of sampling devices, etc., can solve the problems of high strength, high toughness and low yield ratio of steel plates, large residual stress at the end of steel plate shearing, and easy cracks on the end surface of steel plates, etc., to achieve improved Production efficiency, reducing the impact of end stress, and controllable product quality
- Summary
- Abstract
- Description
- Claims
- Application Information
AI Technical Summary
Problems solved by technology
Method used
Examples
Embodiment Construction
[0016] A method for sampling and shearing steel for pressure vessels, adopting TMCP+tempering process to roll and produce steel for pressure vessels:
[0017] 1. After the steel plate is rolled, only the head and tail burrs are cut off and cut in sections, and the burrs are not cut in sections, and then sent to heat treatment;
[0018] 2. After the shot blasting before heat treatment-heat treatment tempering-straightening-cooling process, the steel plate is off-line for cutting and sampling, and the strength of the steel plate is reduced to 600-700MPa after tempering;
[0019] 3. Avoid the end of shear stress, and use the "sample digging" method to sample and analyze the sub-plates obtained after segmental cutting, so as to avoid the influence of shear stress on performance. The so-called "sampling" method means cutting and sampling at a position at least 100mm away from the end of the sub-board under the condition of ensuring the fixed length;
[0020] 4. After the performan...
PUM
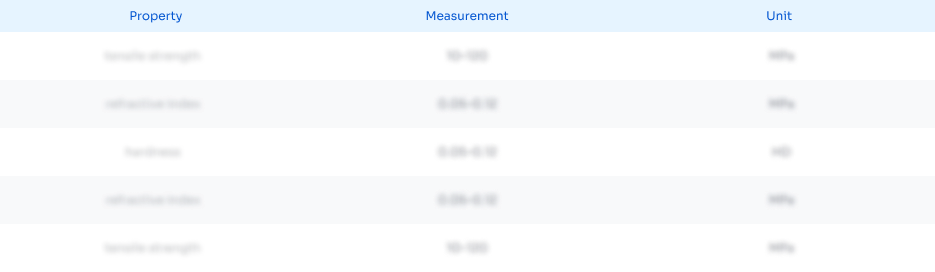
Abstract
Description
Claims
Application Information

- Generate Ideas
- Intellectual Property
- Life Sciences
- Materials
- Tech Scout
- Unparalleled Data Quality
- Higher Quality Content
- 60% Fewer Hallucinations
Browse by: Latest US Patents, China's latest patents, Technical Efficacy Thesaurus, Application Domain, Technology Topic, Popular Technical Reports.
© 2025 PatSnap. All rights reserved.Legal|Privacy policy|Modern Slavery Act Transparency Statement|Sitemap|About US| Contact US: help@patsnap.com