Continuous winding vacuum coating method for ultrathin base film
A technology of vacuum coating and vacuum coating machine, used in vacuum evaporation coating, sputtering coating, ion implantation coating and other directions, can solve the impact of equipment and flexible coating product quality, affect production efficiency and product quality, thin film base film Fracture and other problems, to achieve the effect of high quality, high yield and quality assurance
- Summary
- Abstract
- Description
- Claims
- Application Information
AI Technical Summary
Problems solved by technology
Method used
Image
Examples
Embodiment Construction
[0046] Embodiments of the present invention will be further described below in conjunction with the accompanying drawings. It should be understood that the specific embodiments described here are only used to illustrate and explain the present invention, not to limit the present invention.
[0047] figure 1 Shown is a schematic structural view of an embodiment of a double-sided multi-station winding vacuum coating machine used in the present invention, the vacuum coating machine mainly includes an unwinding chamber 109, a vacuum evaporation coating chamber, and a magnetron sputtering coating chamber 104. The winding chamber 108 and the winding system. In this embodiment, there are 6 vacuum evaporation coating chambers, which are respectively the vacuum evaporation coating chamber 101, the vacuum evaporation coating chamber 102, the vacuum evaporation coating chamber 103, and the vacuum evaporation coating chamber. Chamber 105, vacuum evaporation coating chamber 106 and vacuum...
PUM
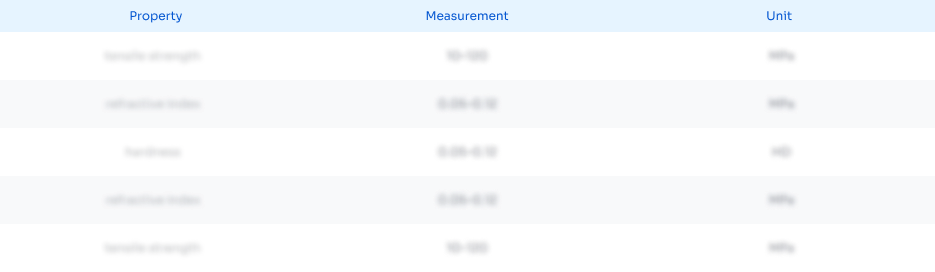
Abstract
Description
Claims
Application Information

- R&D
- Intellectual Property
- Life Sciences
- Materials
- Tech Scout
- Unparalleled Data Quality
- Higher Quality Content
- 60% Fewer Hallucinations
Browse by: Latest US Patents, China's latest patents, Technical Efficacy Thesaurus, Application Domain, Technology Topic, Popular Technical Reports.
© 2025 PatSnap. All rights reserved.Legal|Privacy policy|Modern Slavery Act Transparency Statement|Sitemap|About US| Contact US: help@patsnap.com