High-precision motor multi-physics field coupling simulation calculation method
A simulation calculation and multi-physics technology, applied in calculation, electrical digital data processing, computer-aided design, etc., can solve problems such as motor temperature rise, large calculation error of motor temperature rise distribution, and inaccurate calculation of electromagnetic loss
- Summary
- Abstract
- Description
- Claims
- Application Information
AI Technical Summary
Problems solved by technology
Method used
Image
Examples
specific Embodiment
[0042] Specific embodiments of the present invention are as follows, as Figure 1-3 Including the following steps:
[0043]S1. Import the model parameters into the software to obtain the test parameters, accurately calculate the calculation parameters of the electromagnet loss through the deep learning algorithm, and obtain the electromagnetic simulation model and loss calculation model of the motor, and perform a single coupling simulation calculation of the temperature-stress field on the motor And the two-way strong coupling simulation calculation of the electromagnetic-temperature field;
[0044] S2. Set the number of iterations and error rate, and perform two-way strong coupling simulation calculation of the electromagnetic-temperature field on the motor;
[0045] S3. After the temperature of the motor in S2 converges, the simulation results are output. The simulation results include the distribution diagram of the motor flux density, the distribution diagram of the moto...
PUM
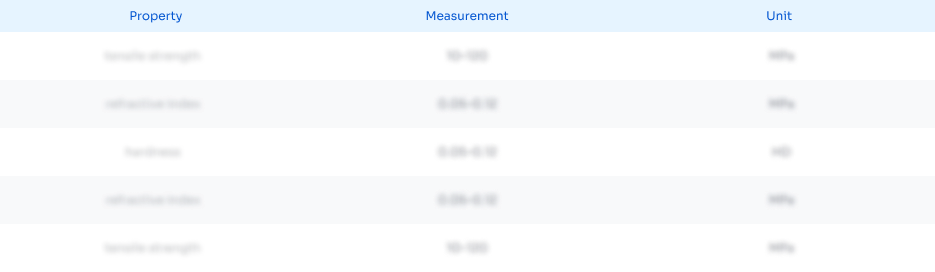
Abstract
Description
Claims
Application Information

- Generate Ideas
- Intellectual Property
- Life Sciences
- Materials
- Tech Scout
- Unparalleled Data Quality
- Higher Quality Content
- 60% Fewer Hallucinations
Browse by: Latest US Patents, China's latest patents, Technical Efficacy Thesaurus, Application Domain, Technology Topic, Popular Technical Reports.
© 2025 PatSnap. All rights reserved.Legal|Privacy policy|Modern Slavery Act Transparency Statement|Sitemap|About US| Contact US: help@patsnap.com