Efficient desulfurizer taking industrial waste residues as active raw material as well as preparation method and application thereof
A technology for industrial waste residue and desulfurization agent, which is applied in the petroleum industry, separation methods, chemical instruments and methods, etc., can solve the problems of inability to meet the fine desulfurization standard and low desulfurization efficiency, and achieve low cost, high economic value and high precision. Effect
- Summary
- Abstract
- Description
- Claims
- Application Information
AI Technical Summary
Problems solved by technology
Method used
Examples
Embodiment 1
[0027] (1) Catalyst preparation
[0028] Screen and weigh 50g of 100-200mesh fly ash powder, 11.25g of ZnO powder, Fe 2 o 3 Add 11.25g of powder, 11.25g of CaO powder and 11.25g of MgO powder, add 5g of PVA and 40g of water, stir and mix evenly to obtain a mixture. The mixture was formed by extrusion molding, and a strip sample with a diameter of 3mm was extruded by an extruder, and dried at 60°C for 10 hours to obtain a finished desulfurizer. Crush the catalyst and screen the 10-20 mesh catalyst for use.
[0029] (2) Desulfurization agent performance test
[0030] Take a small sample of 7mL desulfurizer and put it into the desulfurization performance evaluation reaction device. The inner diameter of the U-shaped tube in the evaluation reaction device is 10mm, and the simulated gas is passed through for activity evaluation. The composition of the simulated gas is: H 2 S(2000ppm 15mL / min), H 2 (20mL / min), N 2 (200mL / min), catalytic temperature 240°C. Record the H in th...
Embodiment 2
[0032] (1) Catalyst preparation
[0033] Screen and weigh 50g of 100-200mesh carbide slag powder, 3.75g of ZnO powder, Fe 2 o3 Add 3.75g of powder, 18.75g of CaO powder and 18.75g of MgO powder, add 5g of PEO and 40g of water, stir and mix evenly to obtain a mixture. The mixture was extruded by an extrusion molding process, and a strip sample with a diameter of 3 mm was extruded by an extruder, and dried at 80° C. for 12 hours to obtain a finished desulfurizer. Crush the catalyst and screen the 10-20 mesh catalyst for use.
[0034] (2) Desulfurization agent performance test
[0035] Take a small sample of 7mL desulfurizer and put it into the desulfurization performance evaluation reaction device. The inner diameter of the U-shaped tube in the evaluation reaction device is 10mm, and the simulated gas is passed through for activity evaluation. The composition of the simulated gas is: H 2 S(2000ppm 15mL / min), H 2 (20mL / min), N 2 (200mL / min), catalytic temperature 240°C. R...
Embodiment 3
[0037] (1) Catalyst preparation
[0038] Screen and weigh 90g of 100-200mesh fly ash powder, 0.75g of ZnO powder, Fe 2 o 3 Add 3.75g of powder, 3.75g of CaO powder and 0.75g of MgO powder, add 1g of CMC and 40g of water, stir and mix evenly to obtain a mixture. The mixture was extruded by an extrusion molding process, and a strip sample with a diameter of 3 mm was extruded by an extruder, and dried at 60° C. for 14 hours to obtain a finished desulfurizer. Crush the catalyst and screen the 10-20 mesh catalyst for use.
[0039] (2) Desulfurization agent performance test
[0040] Take a small sample of 7mL desulfurizer and put it into the desulfurization performance evaluation reaction device. The inner diameter of the U-shaped tube in the evaluation reaction device is 10mm, and the simulated gas is passed through for activity evaluation. The composition of the simulated gas is: H 2 S(2000ppm 15mL / min), H 2 (20mL / min), N 2 (200mL / min), catalytic temperature 240°C. Record...
PUM
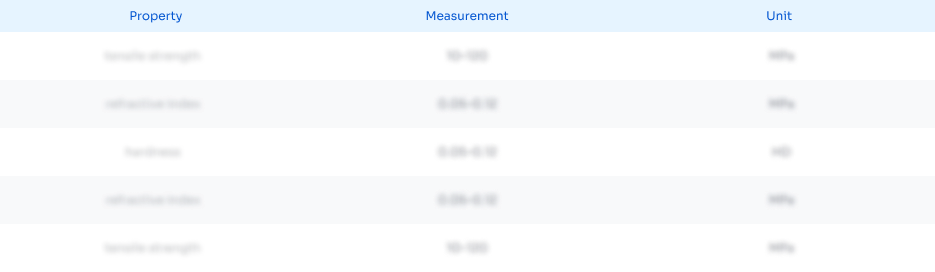
Abstract
Description
Claims
Application Information

- Generate Ideas
- Intellectual Property
- Life Sciences
- Materials
- Tech Scout
- Unparalleled Data Quality
- Higher Quality Content
- 60% Fewer Hallucinations
Browse by: Latest US Patents, China's latest patents, Technical Efficacy Thesaurus, Application Domain, Technology Topic, Popular Technical Reports.
© 2025 PatSnap. All rights reserved.Legal|Privacy policy|Modern Slavery Act Transparency Statement|Sitemap|About US| Contact US: help@patsnap.com