A relief valve suitable for compensating hydraulic power in back pressure condition
A technology of hydraulic power and overflow valve, which is applied in the field of aerospace servo system, can solve the problems of high cost, spool reset jamming, etc., and achieve the effect of compact structure, eliminating jamming, and high precision of voltage regulation
- Summary
- Abstract
- Description
- Claims
- Application Information
AI Technical Summary
Problems solved by technology
Method used
Image
Examples
Embodiment Construction
[0018] In order to enable those skilled in the art to better understand the solution of the present invention, the following in conjunction with the attached Figure 1~6 The present invention is described in further detail.
[0019] A relief valve suitable for compensating hydraulic power in working conditions with back pressure, comprising a spool 8, a valve body 9 that slides with the spool 8 and fits on the outside of the spool 8, and a spring blocked on one side of the valve body 9 The end cover 1 and the main spring 4 arranged between the spring end cover 1 and the valve core 8; the valve body 9 is provided with an inlet A11, an outlet B10, an overflow port C14 and an oil discharge port D16 for connecting the oil tank, A chamber e18, an oil chamber f6 and a spring chamber g15 are formed between the valve body 9 and the valve core 8, the overflow port C14 communicates with the oil chamber f6, and the valve core 8 and the valve body 9 are provided at the inlet end of the oi...
PUM
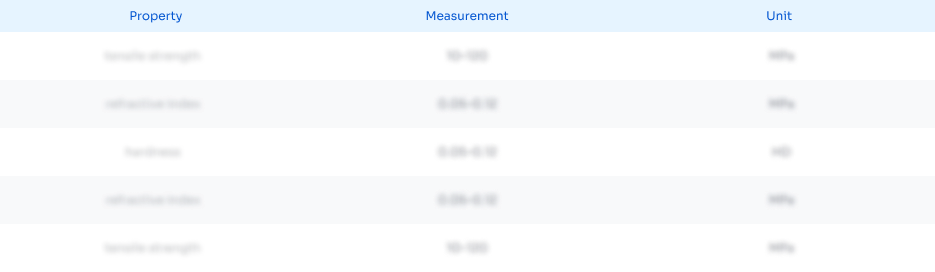
Abstract
Description
Claims
Application Information

- R&D
- Intellectual Property
- Life Sciences
- Materials
- Tech Scout
- Unparalleled Data Quality
- Higher Quality Content
- 60% Fewer Hallucinations
Browse by: Latest US Patents, China's latest patents, Technical Efficacy Thesaurus, Application Domain, Technology Topic, Popular Technical Reports.
© 2025 PatSnap. All rights reserved.Legal|Privacy policy|Modern Slavery Act Transparency Statement|Sitemap|About US| Contact US: help@patsnap.com