Curve fiber composite structure aeroelasticity optimization method considering local buckling
A kind of aeroelasticity, fiber technology, applied in design optimization/simulation, instrument, geometric CAD, etc., can solve the problems of deviation of analysis results, lack of reference significance of analysis results, and inability to use automatic optimization programs.
- Summary
- Abstract
- Description
- Claims
- Application Information
AI Technical Summary
Problems solved by technology
Method used
Image
Examples
Embodiment Construction
[0061] In order to facilitate those of ordinary skill in the art to understand and implement the present invention, the present invention will be further described in detail and in-depth below in conjunction with the accompanying drawings.
[0062] The present invention is a double-layer optimization algorithm suitable for the aeroelastic tailoring of curved fiber composite airfoil structures, such as figure 1 As shown, considering the calculation efficiency and analysis accuracy at the same time, the overall wing model with medium density mesh is used to analyze the aeroelastic parameters, such as static deformation, flutter velocity and composite failure, etc.; The panel model performs local buckling analysis of the airfoil to accurately analyze and predict the local buckling characteristics of the structure. The boundary conditions of the local buckling analysis are based on the static aeroelastic analysis results. Due to the different grid densities, an appropriate interpo...
PUM
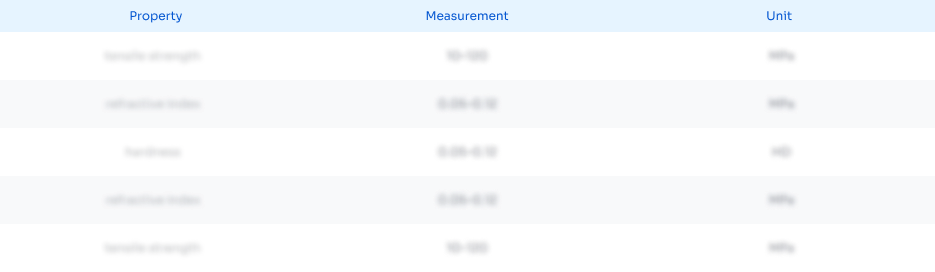
Abstract
Description
Claims
Application Information

- R&D Engineer
- R&D Manager
- IP Professional
- Industry Leading Data Capabilities
- Powerful AI technology
- Patent DNA Extraction
Browse by: Latest US Patents, China's latest patents, Technical Efficacy Thesaurus, Application Domain, Technology Topic, Popular Technical Reports.
© 2024 PatSnap. All rights reserved.Legal|Privacy policy|Modern Slavery Act Transparency Statement|Sitemap|About US| Contact US: help@patsnap.com