High-flame-retardant antistatic yarn and processing method thereof
An anti-static and high flame retardant technology, applied in the manufacture of flame-retardant fibers, fire-retardant and flame-retardant filaments, and conductive/anti-static filaments. It can solve the problems of components destroying circuits, stimulating nerves, and easily generating static electricity.
- Summary
- Abstract
- Description
- Claims
- Application Information
AI Technical Summary
Problems solved by technology
Method used
Image
Examples
Embodiment 1
[0038] A high flame-retardant antistatic yarn, comprising the following raw materials in parts by weight:
[0039] 100 parts of polybutylene terephthalate / adipate, 1 part of polyethylene glycol, 0.6 parts of antistatic agent, 3 parts of flame retardant, 70 parts of wool fiber, 70 parts of cotton fiber and 100 parts of flame retardant treatment liquid ;
[0040] The high flame retardant antistatic yarn is processed through the following steps:
[0041] In the first step, polybutylene terephthalate / adipate and polyethylene glycol are vacuum-dried separately so that the moisture content is less than 200ppm. After drying, they are blended with antistatic agents and flame retardants. Under the conditions of 250°C and a spinning speed of 800r / min, the screw-type spinning machine performs melt spinning, and after cooling, oiling, pre-drawing, and winding at 700m / min are carried out to obtain polyester fibers;
[0042] The second step is to soak the wool fiber and cotton fiber in th...
Embodiment 2
[0056] A high flame-retardant antistatic yarn, comprising the following raw materials in parts by weight:
[0057] 130 parts of polybutylene terephthalate / adipate, 2 parts of polyethylene glycol, 0.8 parts of antistatic agent, 4 parts of flame retardant, 80 parts of wool fiber, 80 parts of cotton fiber and 150 parts of flame retardant treatment liquid ;
[0058] The high flame retardant antistatic yarn is processed through the following steps:
[0059] In the first step, polybutylene terephthalate / adipate and polyethylene glycol are vacuum-dried separately so that the moisture content is less than 200ppm. After drying, they are blended with antistatic agents and flame retardants. Under the conditions of 270°C and a spinning speed of 1000r / min, the screw-type spinning machine is melt-spun, and after cooling, it is oiled, pre-drawn, and wound at 750m / min to obtain polyester fibers;
[0060] The second step is to soak the wool fiber and cotton fiber in the flame retardant treat...
Embodiment 3
[0074] A high flame-retardant antistatic yarn, comprising the following raw materials in parts by weight:
[0075] 160 parts of polybutylene terephthalate / adipate, 3 parts of polyethylene glycol, 1 part of antistatic agent, 5 parts of flame retardant, 90 parts of wool fiber, 90 parts of cotton fiber and 200 parts of flame retardant treatment liquid ;
[0076] The high flame retardant antistatic yarn is processed through the following steps:
[0077] In the first step, polybutylene terephthalate / adipate and polyethylene glycol are vacuum-dried separately so that the moisture content is less than 200ppm. After drying, they are blended with antistatic agents and flame retardants. Under the conditions of 290°C and a spinning speed of 1200r / min, the screw-type spinning machine performs melt spinning, and after cooling, oiling, pre-drawing, and 800m / min winding are carried out to obtain polyester fibers;
[0078] The second step is to soak the wool fiber and cotton fiber in the fl...
PUM
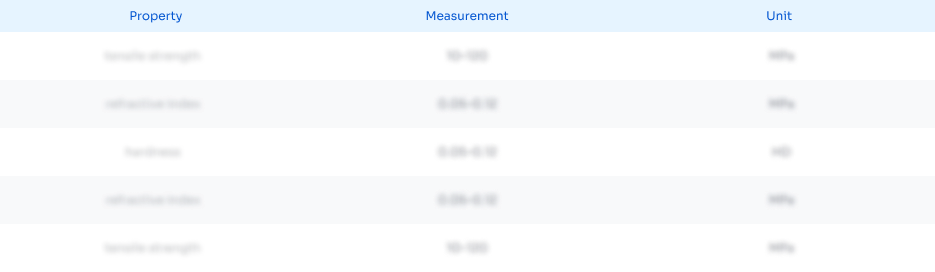
Abstract
Description
Claims
Application Information

- R&D
- Intellectual Property
- Life Sciences
- Materials
- Tech Scout
- Unparalleled Data Quality
- Higher Quality Content
- 60% Fewer Hallucinations
Browse by: Latest US Patents, China's latest patents, Technical Efficacy Thesaurus, Application Domain, Technology Topic, Popular Technical Reports.
© 2025 PatSnap. All rights reserved.Legal|Privacy policy|Modern Slavery Act Transparency Statement|Sitemap|About US| Contact US: help@patsnap.com