Face gear tooth scraping machining method
A processing method and face gear technology, applied in gear tooth manufacturing devices, metal processing equipment, belts/chains/gears, etc., can solve the problems of low processing efficiency, limited promotion, and inability to process internal bevel gears, etc., and achieve high processing The effect of precision and high productivity
- Summary
- Abstract
- Description
- Claims
- Application Information
AI Technical Summary
Problems solved by technology
Method used
Image
Examples
Embodiment Construction
[0025] In order to have a clearer understanding of the technical features, purposes and effects of the present invention, the specific implementation manners of the present invention will now be described in detail with reference to the accompanying drawings.
[0026] The material removal mechanism of the surface gear skiving processing method of the present invention is consistent with the cylindrical gear skiving process, both based on the relative slippage of the tooth surface of the staggered shaft transmission, but the processing principle is very different from the cylindrical gear skiving process. The cylindrical gear turning process is based on a spatially staggered axis helical gear transmission, that is, the tool and workpiece form a spatial helical gear pair. However, this method is a space staggered axial surface worm drive, that is, the tool and the workpiece form a space cylindrical worm pair, such as figure 1 As shown, the face gear skiving is realized by replac...
PUM
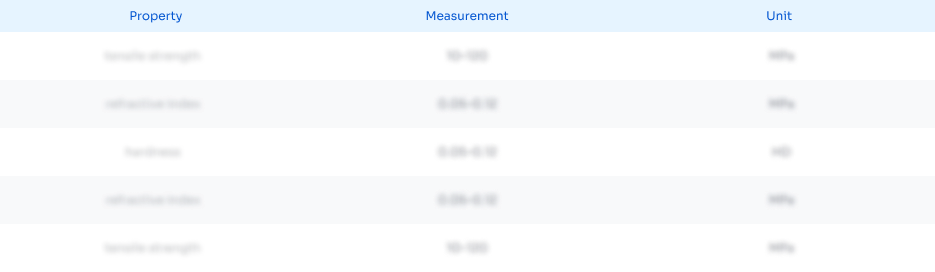
Abstract
Description
Claims
Application Information

- R&D Engineer
- R&D Manager
- IP Professional
- Industry Leading Data Capabilities
- Powerful AI technology
- Patent DNA Extraction
Browse by: Latest US Patents, China's latest patents, Technical Efficacy Thesaurus, Application Domain, Technology Topic, Popular Technical Reports.
© 2024 PatSnap. All rights reserved.Legal|Privacy policy|Modern Slavery Act Transparency Statement|Sitemap|About US| Contact US: help@patsnap.com