Motor rotor shaft sleeve press-in machine
A technology for motor rotor shaft and motor rotor, which is applied in the direction of manufacturing stator/rotor body, etc., can solve problems such as low production efficiency, inability to ensure that the shaft sleeve is in place, and inability to meet the simultaneous pressing of two shafts, and achieve the effect of improving production efficiency.
- Summary
- Abstract
- Description
- Claims
- Application Information
AI Technical Summary
Problems solved by technology
Method used
Image
Examples
Embodiment
[0026] This embodiment proposes a motor rotor sleeve pressing machine, refer to figure 1 , including frame 21, motor rotor positioning block 24 is fixed on the frame 21, the two sides of motor rotor positioning block 24 are symmetrically provided with bushing inserting device 33 and bushing pressing device 32, motor rotor positioning block 24 is provided with motor The rotor pressing block 31, the motor rotor pressing block 31 is used to compress the motor rotor positioned on the motor rotor positioning block 24, and the sleeve inserting device 33 is used to grab the shaft sleeve and initially insert the shaft sleeve into the shaft of the motor rotor Above, the sleeve pressing device 32 is used to press the initially inserted sleeve to a designated position.
[0027] refer to figure 2 , the rotor moving mechanism 26 is vertically connected with a first cylinder 261 for vertical reciprocating motion, and the first cylinder 261 is horizontally connected with a second cylinder ...
PUM
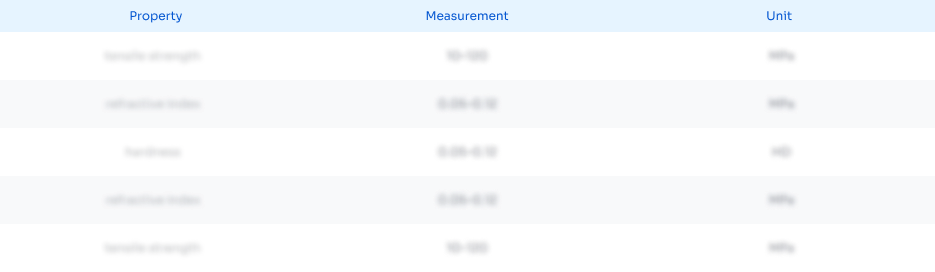
Abstract
Description
Claims
Application Information

- R&D Engineer
- R&D Manager
- IP Professional
- Industry Leading Data Capabilities
- Powerful AI technology
- Patent DNA Extraction
Browse by: Latest US Patents, China's latest patents, Technical Efficacy Thesaurus, Application Domain, Technology Topic, Popular Technical Reports.
© 2024 PatSnap. All rights reserved.Legal|Privacy policy|Modern Slavery Act Transparency Statement|Sitemap|About US| Contact US: help@patsnap.com