Robot polishing and grinding method, robot polishing and grinding device and robot polishing and grinding system
A technology of robots and controllers, applied in manipulators, program-controlled manipulators, manufacturing tools, etc., can solve the problems of limited response bandwidth of the force control system, slow polishing operation rhythm, and adjustment of bonding state, etc., to achieve high polishing operation efficiency , The teaching process is fast and the beat is fast
- Summary
- Abstract
- Description
- Claims
- Application Information
AI Technical Summary
Problems solved by technology
Method used
Image
Examples
Embodiment 1
[0035] Such as figure 1 As shown, the robot polishing method includes the following steps:
[0036] A. The robot performs the first pre-polishing based on several teaching points in the force control mode, and records the polishing trajectory information during the first pre-polishing process.
[0037] B. The robot performs the second pre-polishing based on the polishing track information in the position mode.
[0038] C. Verify whether the polishing effect is feasible.
[0039] D. If the polishing effect is feasible, the robot performs polishing operations in position mode or force control mode according to the polishing track information and the first polishing speed corresponding to the second pre-polishing.
[0040] E. If the polishing effect is not feasible, correct the polishing speed of the second pre-polishing, and the robot will perform the second pre-polishing again based on the corrected polishing speed.
[0041] F. Verify whether the polishing effect is feasible...
Embodiment 2
[0061] Embodiment 2 of the present invention provides a robot polishing device. The robot polishing device includes a force control mode module, a position mode module and a speed control module.
[0062] The force control mode control module is used to enable the robot to perform the first pre-polishing and polishing operations based on several teaching points in the force control mode, and record the polishing trajectory information during the first pre-polishing process. The position mode module is used to make the robot perform the second pre-polishing and polishing operation based on the polishing track information in the position mode.
[0063] The speed regulation module is used for regulating and controlling the polishing speed. Take the polishing method of the robot in the first embodiment as an example. The speed control module can play a role in correcting the polishing speed of the second pre-polishing in step E, and the speed control module can also control the ...
Embodiment 3
[0081] Embodiment 3 of the present invention provides a storage medium, on which a computer program is stored, and the computer program is used to implement the robot polishing method provided in Embodiment 1 when executed by a controller.
PUM
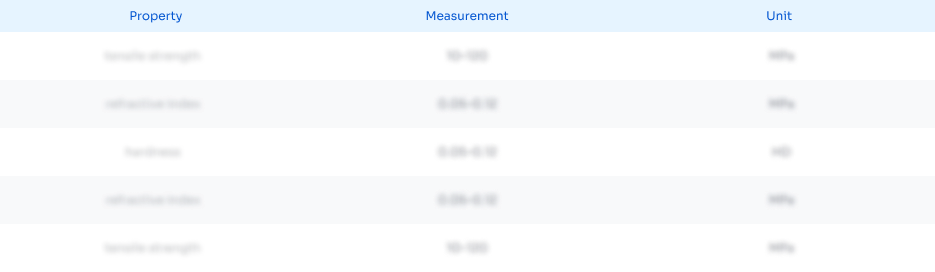
Abstract
Description
Claims
Application Information

- Generate Ideas
- Intellectual Property
- Life Sciences
- Materials
- Tech Scout
- Unparalleled Data Quality
- Higher Quality Content
- 60% Fewer Hallucinations
Browse by: Latest US Patents, China's latest patents, Technical Efficacy Thesaurus, Application Domain, Technology Topic, Popular Technical Reports.
© 2025 PatSnap. All rights reserved.Legal|Privacy policy|Modern Slavery Act Transparency Statement|Sitemap|About US| Contact US: help@patsnap.com