Gas-magnetic hybrid bearing error compensation method based on electromagnetic force adjustment
An error compensation, gas-magnetic hybrid technology, applied in air-cushion bearings, bearings, shafts and bearings, etc., can solve the problems of complex control, high difficulty in manufacturing and low reliability of non-actively controlled gas static pressure support, and reduce the The effect of manufacturing difficulty, improving stiffness, and reducing errors
- Summary
- Abstract
- Description
- Claims
- Application Information
AI Technical Summary
Problems solved by technology
Method used
Image
Examples
Embodiment
[0031] An error compensation method for an aeromagnetic hybrid support based on electromagnetic force adjustment, specifically an open-loop control method for an aeromagnetic hybrid support, performing static calibration and dynamic calibration in sequence, including the following steps:
[0032] 1) Static calibration
[0033] a. Drive the turntable or guide rail to various positions and keep it stationary;
[0034] b. Measure the stiffness of the air bearing point by point, and fit the smooth stiffness curve at multiple points, such as figure 1 shown;
[0035] c. Measure at least one of the rotation error, straightness error, and shaft pendulum error point by point, and fit the smooth error curve at multiple points, such as figure 2 shown;
[0036] d. According to the rotation error, straightness error, shaft pendulum error and stiffness of each position, the force-displacement conversion algorithm is adopted, the controller outputs the corresponding electromagnetic force...
PUM
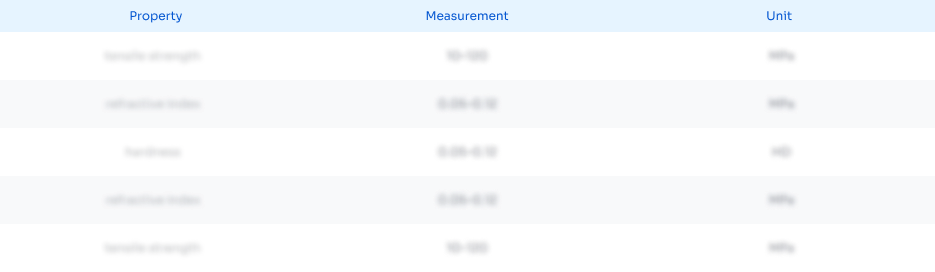
Abstract
Description
Claims
Application Information

- Generate Ideas
- Intellectual Property
- Life Sciences
- Materials
- Tech Scout
- Unparalleled Data Quality
- Higher Quality Content
- 60% Fewer Hallucinations
Browse by: Latest US Patents, China's latest patents, Technical Efficacy Thesaurus, Application Domain, Technology Topic, Popular Technical Reports.
© 2025 PatSnap. All rights reserved.Legal|Privacy policy|Modern Slavery Act Transparency Statement|Sitemap|About US| Contact US: help@patsnap.com