Rotating joint and robot
A technology of rotating joints and joints, which is used in manipulators, transportation and packaging, stacking of objects, etc., can solve the problems of increased stress at the rotating joints of robots, uneven force on the rotating joints of robots, and unreasonable structural design of robots. Achieve the effect of shortening maintenance time, avoiding premature wear and improving design depth
- Summary
- Abstract
- Description
- Claims
- Application Information
AI Technical Summary
Problems solved by technology
Method used
Image
Examples
Embodiment Construction
[0056] see Figure 1 to Figure 6 , a rotary joint in this embodiment, including a first joint body 11, a second joint body 12, a rotating shaft, a bearing bush 14, four bearings 15, two covers 16, and two retaining springs 17;
[0057] Specifically, the first joint body 11 is provided with a first hinge hole 111;
[0058] Specifically, the second joint body 12 is provided with a mounting groove 121 for the installation of the first joint body 11; the two sides of the mounting groove 121 are respectively provided with a second hinge hole 122 and a third hinge hole 123; A hinge hole 111 is arranged coaxially with the second hinge hole 122 and the third hinge hole 123;
[0059] Specifically, the rotation shaft is rotatably arranged in the first hinge hole 111 , the second hinge hole 122 and the third hinge hole 123 ;
[0060] Specifically, the inner ring of the bearing pad 14 is sleeved outside the rotating shaft, and the inner ring of the bearing pad 14 is an interference fit ...
PUM
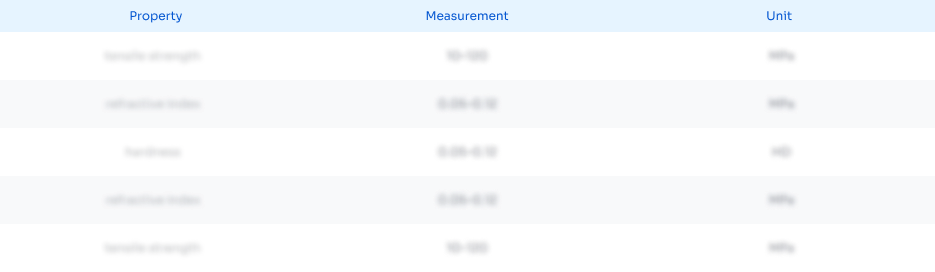
Abstract
Description
Claims
Application Information

- Generate Ideas
- Intellectual Property
- Life Sciences
- Materials
- Tech Scout
- Unparalleled Data Quality
- Higher Quality Content
- 60% Fewer Hallucinations
Browse by: Latest US Patents, China's latest patents, Technical Efficacy Thesaurus, Application Domain, Technology Topic, Popular Technical Reports.
© 2025 PatSnap. All rights reserved.Legal|Privacy policy|Modern Slavery Act Transparency Statement|Sitemap|About US| Contact US: help@patsnap.com