Method for stably coiling ultrathin-specification checkered plate
A patterned plate and specification technology, applied in the field of stable coiling of ultra-thin patterned plates, can solve the problems of complex plate deformation mechanism, increased roller consumption, and reduced effective operation rate.
- Summary
- Abstract
- Description
- Claims
- Application Information
AI Technical Summary
Problems solved by technology
Method used
Image
Examples
Embodiment
[0026] In this example, the production mark of strip steel is GR3180F2, the specification is changed from 1.5mm×1000mm to 1.2mm×1000mm, the target coiling temperature is 590°C, and the measured temperature range is 571°C~613°C at 590°C±30°C scope.
[0027] The method for stable coiling of the ultra-thin specification checkered plate of the present embodiment comprises the following steps:
[0028] Step 1. In the finish rolling stage, determine whether the piece of strip steel is variable-thickness rolling. If it is variable-thickness rolling, according to the initial strip thickness and the target thickness, step 2-step 5 is performed in turn during the coiling stage. In this embodiment, the specification of the steel strip is changed from 1.5mm×1000mm to 1.2mm×1000mm, so it is variable thickness rolling, and step 2-step 5 are performed in sequence during the coiling stage.
[0029] If it is not variable thickness rolling, the target thickness is used as the initial strip thi...
PUM
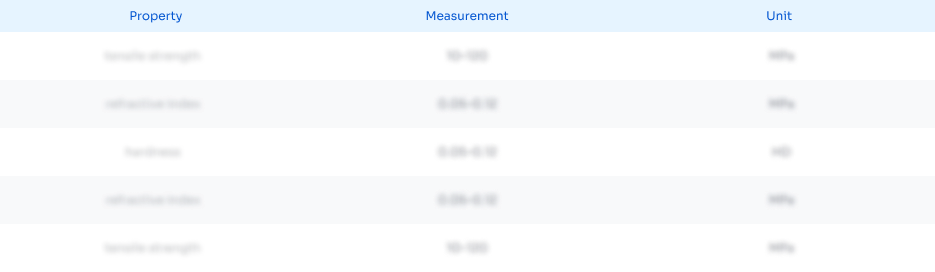
Abstract
Description
Claims
Application Information

- Generate Ideas
- Intellectual Property
- Life Sciences
- Materials
- Tech Scout
- Unparalleled Data Quality
- Higher Quality Content
- 60% Fewer Hallucinations
Browse by: Latest US Patents, China's latest patents, Technical Efficacy Thesaurus, Application Domain, Technology Topic, Popular Technical Reports.
© 2025 PatSnap. All rights reserved.Legal|Privacy policy|Modern Slavery Act Transparency Statement|Sitemap|About US| Contact US: help@patsnap.com