Coal-fired multi-composite spinel material and its preparation method and application
A spinel and aluminum-magnesium spinel technology is applied in the field of coal-fired multi-composite spinel materials and their preparation, which can solve the problems of short service life and incompetence, and achieve high refractoriness, prolong service life, The effect of low apparent porosity
- Summary
- Abstract
- Description
- Claims
- Application Information
AI Technical Summary
Problems solved by technology
Method used
Image
Examples
preparation example Construction
[0055] The present invention also provides a method for preparing the coal-fired multi-composite spinel material, comprising the following steps:
[0056] The raw materials are mixed according to the proportion, molded under high pressure, baked at 80-150 DEG C for 12-48 hours, and then sintered at 1300-1650 DEG C for 40-50 hours.
[0057] In a specific embodiment of the present invention, the high pressure forming is performed in a mold. Further, the pressure of the high pressure forming is 630T to 1250T.
[0058] The present invention also provides the application of any one of the above coal-fired multi-composite spinel materials in refractory materials.
[0059] In a specific embodiment of the present invention, the refractory material is a furnace lining material. Further, the furnace lining material is the furnace lining material of the coal-injected sleeve lime kiln. However, this lining material can not only be used in coal-injection sleeve lime kilns, but also in r...
Embodiment 1
[0061] The present embodiment provides a method for preparing a coal-fired multi-composite spinel material, comprising the following steps:
[0062] (1) In parts by weight, weigh 5 parts of magnesium-iron-aluminum composite spinel, 12 parts of aluminum-magnesium spinel, 50 parts of chromium-containing materials, 6 parts of zirconium-containing materials, 15 parts of corundum materials, and 5 parts of binders , α-Al 2 O 3 5 parts of micropowder and 2 parts of water;
[0063] Among them, in the magnesium-iron-aluminum composite spinel, the content of MgO is 5wt%, and the Al 2 O 3 The content is 85wt%, Fe 2 O 3 The content of Al-Mg is 5wt%; in Al-Mg spinel, Al 2 O 3 The content of MgO is 91wt%, and the content of MgO is 6%; the chromium-containing material is a low-chromium-chromium corundum and an aluminum-chromium eutectic with a mass ratio of 1:1. In the low-chromium-chromium corundum, Cr 2 O 3 The content is 1wt%, in the aluminum-chromium eutectic, Cr 2 O 3 The con...
Embodiment 2
[0067] The present embodiment provides a method for preparing a coal-fired multi-composite spinel material, comprising the following steps:
[0068] (1) In parts by weight, weigh 12 parts of magnesium-iron-aluminum composite spinel, 5 parts of aluminum-magnesium spinel, 40 parts of chromium-containing materials, 10 parts of zirconium-containing materials, 19 parts of corundum materials, and 2 parts of binders , α-Al 2 O 3 10 parts of micropowder and 2 parts of water;
[0069] Among them, in the magnesium-iron-aluminum composite spinel, the content of MgO is 8wt%, and the Al 2 O 3 The content is 88wt%, Fe 2 O 3 The content of Al-Mg is 3wt%; in Al-Mg spinel, Al 2 O 3 The content of MgO is 90wt%, and the content of MgO is 5wt%; the chromium-containing material is low-chromium-chromium corundum and aluminum-chromium eutectic with a mass ratio of 1:1. In low-chromium-chromium corundum, Cr 2 O 3 The content of 2wt%, aluminum-chromium eutectic, Cr 2 O 3 The content of zirc...
PUM
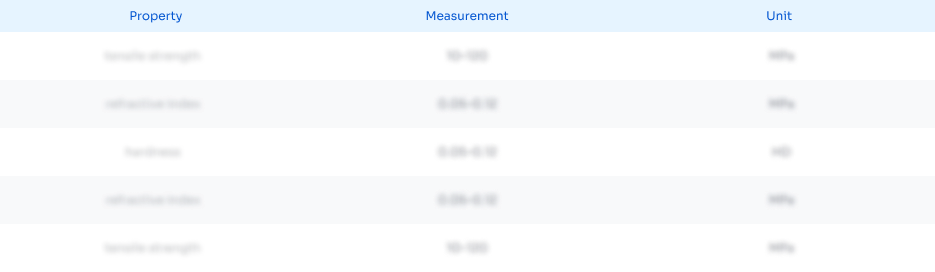
Abstract
Description
Claims
Application Information

- R&D Engineer
- R&D Manager
- IP Professional
- Industry Leading Data Capabilities
- Powerful AI technology
- Patent DNA Extraction
Browse by: Latest US Patents, China's latest patents, Technical Efficacy Thesaurus, Application Domain, Technology Topic, Popular Technical Reports.
© 2024 PatSnap. All rights reserved.Legal|Privacy policy|Modern Slavery Act Transparency Statement|Sitemap|About US| Contact US: help@patsnap.com