A digital twin-based near-physical simulation integrated debugging method and system
A technology of physical simulation and debugging method, applied in the direction of control/regulation system, signal transmission system, image data processing, etc., can solve the performance reduction of production line system, increase of cost, functional integrity of automation equipment, accuracy of control logic, performance reliability Can not meet production needs and other problems
- Summary
- Abstract
- Description
- Claims
- Application Information
AI Technical Summary
Problems solved by technology
Method used
Image
Examples
Embodiment Construction
[0072] Embodiments of the present invention are described in detail below, and examples of the embodiments are shown in the drawings, wherein the same or similar reference numerals denote the same or similar elements or elements having the same or similar functions throughout. The embodiments described below by referring to the figures are exemplary only for explaining the present invention and should not be construed as limiting the present invention.
[0073] The following disclosure provides many different embodiments or examples for implementing different structures of embodiments of the present invention. In order to simplify the disclosure of the embodiments of the present invention, components and arrangements of specific examples are described below. Of course, they are only examples and are not intended to limit the invention. Furthermore, embodiments of the present invention may repeat reference numerals and / or reference letters in different instances, such repetiti...
PUM
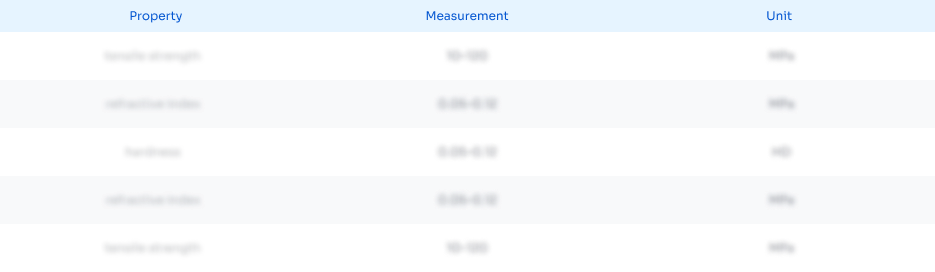
Abstract
Description
Claims
Application Information

- R&D
- Intellectual Property
- Life Sciences
- Materials
- Tech Scout
- Unparalleled Data Quality
- Higher Quality Content
- 60% Fewer Hallucinations
Browse by: Latest US Patents, China's latest patents, Technical Efficacy Thesaurus, Application Domain, Technology Topic, Popular Technical Reports.
© 2025 PatSnap. All rights reserved.Legal|Privacy policy|Modern Slavery Act Transparency Statement|Sitemap|About US| Contact US: help@patsnap.com