A Low-Complexity Control Method for Asymmetric Servo-Hydraulic Position Tracking System
A hydraulic system and complex control technology, applied in the direction of adaptive control, general control system, control/regulation system, etc., can solve the problems of uncertain parameters, occurrence of dangerous hardware, large amount of calculation, etc., and achieve a small degree of phase lag and easy The effect of engineering realization and easy real-time control
- Summary
- Abstract
- Description
- Claims
- Application Information
AI Technical Summary
Problems solved by technology
Method used
Image
Examples
Embodiment Construction
[0108] In order to make the technical solutions and advantages of the present invention more clear, the technical solutions in the embodiments of the present invention are clearly and completely described below in conjunction with the drawings in the embodiments of the present invention:
[0109] The specific embodiment of the present invention will be further described below in conjunction with accompanying drawing:
[0110] figure 1 It is a flow chart of a low-complexity control method for an asymmetrical servo hydraulic position tracking system of the present invention: a low-complexity control method for an asymmetrical servo-hydraulic position tracking system, including the following steps: S1: Establish a single-outlet servo hydraulic system system model; figure 2 is the model block diagram of the single-rod servo hydraulic system; S2: Based on the model of the single-rod servo hydraulic system, the controller of the single-rod servo hydraulic system is designed using ...
PUM
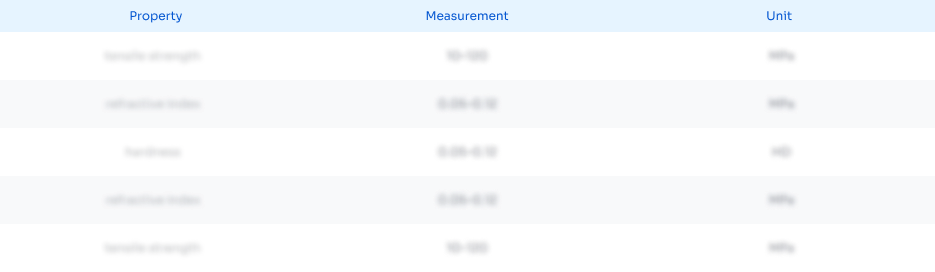
Abstract
Description
Claims
Application Information

- Generate Ideas
- Intellectual Property
- Life Sciences
- Materials
- Tech Scout
- Unparalleled Data Quality
- Higher Quality Content
- 60% Fewer Hallucinations
Browse by: Latest US Patents, China's latest patents, Technical Efficacy Thesaurus, Application Domain, Technology Topic, Popular Technical Reports.
© 2025 PatSnap. All rights reserved.Legal|Privacy policy|Modern Slavery Act Transparency Statement|Sitemap|About US| Contact US: help@patsnap.com