Vehicle suspension with adjustable shock absorber damping coefficient and collaborative design method
A damping coefficient and vehicle suspension technology, applied in the field of rail vehicles, can solve the problems that the parameters cannot be adjusted and the performance is difficult to meet people's higher comfort and stability of rail vehicle operation, and achieve the effect of improving safety and comfort.
- Summary
- Abstract
- Description
- Claims
- Application Information
AI Technical Summary
Problems solved by technology
Method used
Image
Examples
Embodiment 1
[0056] Such as figure 1 As shown, a vehicle suspension with adjustable damping coefficient of the shock absorber described in this application includes a spring 1, an adjustable damping shock absorber 2 and an inerter 3, the spring 1, the adjustable damping shock absorber The container 2 and the inerter 3 are arranged in parallel with each other.
[0057] On the basis of the above, in a further preferred manner, the damping adjustable shock absorber 2 is an electromagnetic eddy current shock absorber.
[0058] A vehicle suspension with adjustable damping coefficient of the shock absorber described in the present application includes a spring, an adjustable damping shock absorber and an inerter, the spring, the adjustable damping shock absorber and the inerter set in parallel with each other. The damping adjustable shock absorber is an electromagnetic eddy current shock absorber, its damping coefficient can be adjusted by adjusting the exciting current of the electromagnet, a...
Embodiment 2
[0065] Such as figure 2 and 3 As shown, this embodiment discloses a collaborative design method for the spring stiffness K of the spring 1 and the maximum damping coefficient c of the damping adjustable shock absorber 2 max Collaborative design with the inertial mass I of the inertial container 3, the collaborative design method comprises the following steps:
[0066] S1. According to the principle of dynamics, a vertical six-degree-of-freedom dynamics model is established based on a vehicle suspension with adjustable damping coefficient of the shock absorber described in this application, such as figure 2 shown;
[0067] S2. According to the basic parameters of the vehicle, as well as various conventional loads and ultimate loads at both ends of the vehicle suspension under different working conditions, and based on the vertical six-degree-of-freedom dynamic model, calculate the load time history function value F under the corresponding working conditions t ; Wherein, th...
Embodiment 3
[0094] Such as figure 2 and 4 As shown, this embodiment discloses a collaborative design method. The response matrix in Embodiment 1 can also be implemented in a cyclic calculation method, that is, the spring stiffness K of the spring 1, the adjustable damping Maximum damping coefficient c of shock absorber 2 max and the inertial mass I of the inerter 3, first select two of them as fixed values, and then change the third parameter as a variable to calculate the corresponding overall response value Ψ, and then loop in turn to determine two of the parameters , change the third parameter as a variable, and compare each cycle, and finally find the minimum value Ψ among all the overall response values Ψ min , the minimum value Ψ min Corresponding spring stiffness K, maximum damping coefficient c max and the inertial mass I are the final design values, which are specifically:
[0095] Step 1. Establish a vertical six-degree-of-freedom dynamics model based on the vehicle susp...
PUM
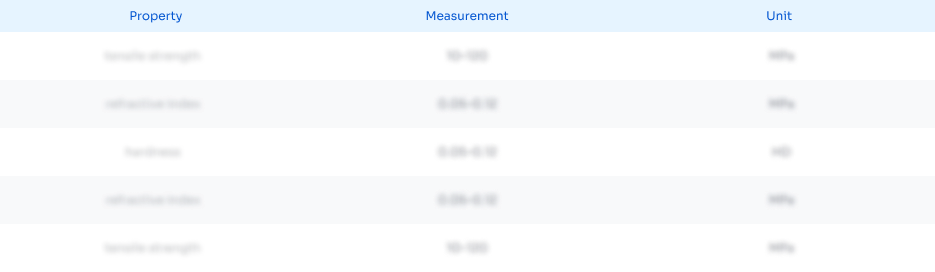
Abstract
Description
Claims
Application Information

- R&D Engineer
- R&D Manager
- IP Professional
- Industry Leading Data Capabilities
- Powerful AI technology
- Patent DNA Extraction
Browse by: Latest US Patents, China's latest patents, Technical Efficacy Thesaurus, Application Domain, Technology Topic, Popular Technical Reports.
© 2024 PatSnap. All rights reserved.Legal|Privacy policy|Modern Slavery Act Transparency Statement|Sitemap|About US| Contact US: help@patsnap.com