Manipulator tail end and method based on intelligent sensing of ultrasonic surface wave contact stress
A technology of ultrasonic surface wave and contact stress, which is applied in the directions of manipulators, measuring force, force/torque/work measuring instruments, etc., which can solve problems such as high cost, limited strength, and inability to reflect local stress conditions at the end of the manipulator and the contact part of the object.
- Summary
- Abstract
- Description
- Claims
- Application Information
AI Technical Summary
Problems solved by technology
Method used
Image
Examples
Embodiment Construction
[0061]The present invention will be further explained below in conjunction with the drawings:
[0062]Such asfigure 1 As shown, the end of a manipulator based on the intelligent sensing of ultrasonic surface wave contact stress of the present invention mainly includes a computer 1, a data acquisition card 2, and an ultrasonic transmitter receiver 3 connected in sequence; the ultrasonic transmitter probe 4 and the ultrasonic receiver probe 6 are both Connect to the ultrasonic transmitter receiver 3 interface; the manipulator must use a special cylindrical end 5A or a spherical end 5B; a probe holder 7 is installed on the finger end side plane to adjust and fix the position of the probe on the upper and lower planes of the end.
[0063]The end of the manipulator based on the intelligent sensing of ultrasonic surface wave contact stress is characterized in that it includes a pair of matching mechanical fingers as a clamping mechanism. The front end of the mechanical fingers is a cylindrical ...
PUM
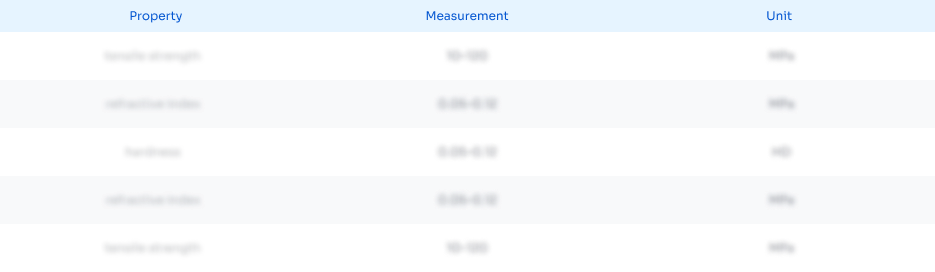
Abstract
Description
Claims
Application Information

- R&D
- Intellectual Property
- Life Sciences
- Materials
- Tech Scout
- Unparalleled Data Quality
- Higher Quality Content
- 60% Fewer Hallucinations
Browse by: Latest US Patents, China's latest patents, Technical Efficacy Thesaurus, Application Domain, Technology Topic, Popular Technical Reports.
© 2025 PatSnap. All rights reserved.Legal|Privacy policy|Modern Slavery Act Transparency Statement|Sitemap|About US| Contact US: help@patsnap.com