Flue gas purification method
A flue gas purification and flue gas technology, which is applied in the field of flue gas purification, can solve the problems of large wind resistance and low liquid-gas ratio of the Venturi tube, and achieve the effects of high liquid-gas ratio, large spray water volume, and moderate wind resistance
- Summary
- Abstract
- Description
- Claims
- Application Information
AI Technical Summary
Problems solved by technology
Method used
Image
Examples
Embodiment 1
[0037] like figure 1 Shown, a kind of flue gas purification method comprises the following steps:
[0038] S1. Lead the flue gas from the air inlet pipe into the cyclone dust collection section 1 to remove large particles in the flue gas;
[0039] S2. The pretreatment section 2 where the flue gas after removing the large particles goes upwards, uses the nozzle 10 to spray the flue gas to cool down, remove acid and remove small particles, and the wind speed of the pretreatment section 2 is controlled at 8-12m / s;
[0040] S3. The pretreated flue gas enters the dehydration section 3 upwards for water droplet settlement treatment, and the wind speed of the dehydration section 3 is less than or equal to 4m / s;
[0041] S4. The flue gas that has been treated by water droplet settlement enters the purification section 5 downwards for spray purification treatment, and the wind speed of the purification section 5 is controlled at 20-30m / s;
[0042] S5. The flue gas that has been spray...
Embodiment 2
[0050] like figure 1 As shown, this embodiment is based on Embodiment 1, and the purification section 5 includes an upper connection section, a middle section and a lower connection section, the upper connection section is connected to the air duct 4, and the two ends of the middle section are respectively connected to the upper section is connected with the lower connecting section, the lower connecting section communicates with the water tank 8, the inner diameter of the middle section is smaller than the inner diameter of the upper connecting section, the nozzle 10 is arranged at the entrance of the middle section, and the upper connecting section and the lower connecting section are connected The sections have the same inner diameter, and a spray head 10 is arranged in the lower connecting section.
[0051] In this embodiment, a throat is formed on the purification section 5. After the flue gas enters the purification section 5, the throat is formed due to the sudden reduc...
Embodiment 3
[0053] The lower end of the pretreatment section 2 extends into the water tank 8 through the cyclone dust collection section 1 .
PUM
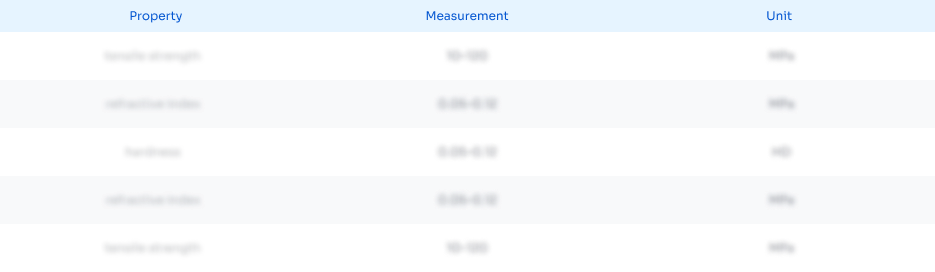
Abstract
Description
Claims
Application Information

- Generate Ideas
- Intellectual Property
- Life Sciences
- Materials
- Tech Scout
- Unparalleled Data Quality
- Higher Quality Content
- 60% Fewer Hallucinations
Browse by: Latest US Patents, China's latest patents, Technical Efficacy Thesaurus, Application Domain, Technology Topic, Popular Technical Reports.
© 2025 PatSnap. All rights reserved.Legal|Privacy policy|Modern Slavery Act Transparency Statement|Sitemap|About US| Contact US: help@patsnap.com