Metal wire machining system and method
A processing system, metal wire technology, applied in metal processing, metal processing equipment, manufacturing tools, etc., can solve problems such as conveying metal wires
- Summary
- Abstract
- Description
- Claims
- Application Information
AI Technical Summary
Problems solved by technology
Method used
Image
Examples
specific Embodiment approach 1
[0033] As shown in the figure, a metal wire processing system includes a support table 1, a shaft seat I101, a shaft I102, a driving limit wheel 103, a groove I104, a rod I105, a pulley I106, a motor I107, a displacement frame 2, shaft II201 and The driven wire pulley 202, the upper end of the support table 1 is fixed to the axle seat I101, and the axle seat I101 is rotatably connected to two symmetrically arranged axles I102. The middle part of the outer ring of the active limiting wheel 103 is provided with a groove I104, and the front ends of the two shafts I102 are fixedly connected to a pulley I106, and the two pulleys I106 are connected through a belt drive, and the output shaft of the motor I107 is fixed to one of the shafts I102. connected, the motor I107 is fixedly connected to the supporting platform 1;
[0034] The upper end of the support table 1 is fixedly connected to two rods I105, the displacement frame 2 is slidably connected to the two rods I105, and the two ...
specific Embodiment approach 2
[0036]As shown in the figure, a groove II 203 is provided in the middle of the outer ring of each moving wire wheel 202 , and the two grooves II 203 are mirror-symmetrical to the two grooves I 104 respectively. Groove II 203 is convenient for metal wires to be directly squeezed in, and is convenient for initial placement, and groove I 104 and groove II 203 are used in combination to increase the holding force for conveying metal wires of different diameters.
specific Embodiment approach 3
[0038] As shown in the figure, the metal wire processing system also includes a guide mechanism, the guide mechanism includes a base 3, a two-way screw 301, a pulley II 302, a shaft seat II 303, a shaft III 304, an auxiliary wheel 305 and a motor II 307, and the base 3 Two bidirectional lead screws 301 are connected by upper rotation, and a pulley II 302 is fixedly connected to the front ends of the two bidirectional lead screws 301, and the two pulleys II 302 are connected through a belt transmission. Threaded on two bi-directional lead screws 301, the two shaft seats II 303 move in opposite directions, and the upper end of each shaft seat II 303 is fixedly connected with two shafts III 304, and the two shafts III 304 are rotatably connected with an auxiliary wheel 305 and motor II 307 The output shaft of the output shaft is fixedly connected to one of the two-way screw 301, and the motor II 307 is fixedly connected to the shaft seat II 303 at the corresponding position. On a...
PUM
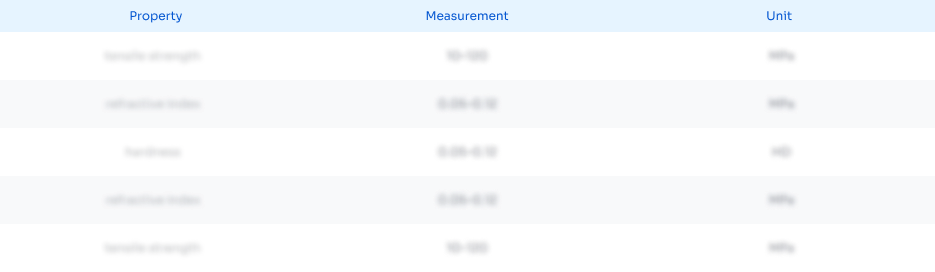
Abstract
Description
Claims
Application Information

- R&D
- Intellectual Property
- Life Sciences
- Materials
- Tech Scout
- Unparalleled Data Quality
- Higher Quality Content
- 60% Fewer Hallucinations
Browse by: Latest US Patents, China's latest patents, Technical Efficacy Thesaurus, Application Domain, Technology Topic, Popular Technical Reports.
© 2025 PatSnap. All rights reserved.Legal|Privacy policy|Modern Slavery Act Transparency Statement|Sitemap|About US| Contact US: help@patsnap.com