Magnesium alloy part tooth-pushing mechanism and mold
A magnesium alloy and sliding mechanism technology, applied in the field of punching dies, can solve the problems of extended production cycle, low product profit margin, and low production efficiency, and achieve the effects of saving procedures, reducing costs, and improving production efficiency
- Summary
- Abstract
- Description
- Claims
- Application Information
AI Technical Summary
Problems solved by technology
Method used
Image
Examples
Embodiment Construction
[0036] The present invention will be further described below in conjunction with embodiment and accompanying drawing.
[0037] Such as figure 1 As shown, a large-scale magnesium alloy product for automobiles is provided with two isolated columns, and a tooth-like structure a is designed on the side walls of the columns. If the existing technology is adopted, the die-casting workpiece is machined and milled on the pillar one by one to get the teeth after being trimmed and removed from the slag bag. The process is long, the beat is slow, and the production cost is high. For this reason, the processing module of the tooth structure is creatively integrated into the mold of the slag bag of the trimming head.
[0038] Such as figure 2 , a gear pushing mechanism for magnesium alloy parts, including a positioning block 12, a tooth cutter 11, and a self-resetting linear sliding mechanism. The positioning block 12 is provided with a positioning hole 13 and a tooth knife through hol...
PUM
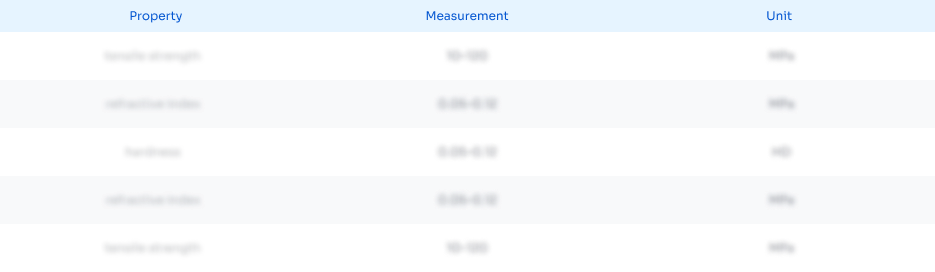
Abstract
Description
Claims
Application Information

- R&D
- Intellectual Property
- Life Sciences
- Materials
- Tech Scout
- Unparalleled Data Quality
- Higher Quality Content
- 60% Fewer Hallucinations
Browse by: Latest US Patents, China's latest patents, Technical Efficacy Thesaurus, Application Domain, Technology Topic, Popular Technical Reports.
© 2025 PatSnap. All rights reserved.Legal|Privacy policy|Modern Slavery Act Transparency Statement|Sitemap|About US| Contact US: help@patsnap.com