Fluid-solid coupling inerter
A technology of fluid-solid coupling and inerter, which is applied in the field of vibration control, can solve problems such as inconvenience, insufficient inertia coefficient, and complex structure of mechanical inerter, and achieve the effect of strengthening engineering value, reducing dynamic response, and ensuring structural safety
- Summary
- Abstract
- Description
- Claims
- Application Information
AI Technical Summary
Problems solved by technology
Method used
Image
Examples
Embodiment
[0037] Such as figure 1 As shown, a fluid-solid coupling inerter, the inerter includes a cylinder 1, a piston 7 that is movably located inside the cylinder 1 in the axial direction and divides the interior of the cylinder 1 into two chambers, and is wound around the The spiral pipe 3 on the outer wall of the cylinder body 1, the two sides of the piston 7 are all vertically provided with a piston rod 2, and the piston rod 2 runs through the cylinder body 1 movably in the axial direction, and the side walls of the two chambers are provided with The pipe port 6 connected to the end of the spiral pipe 3 can be provided with a switch control valve (omitted in the figure), and the inner wall of the chamber is provided with a buffer spring 8. On the side wall in the vertical direction of the body 1, the cylinder body 1 and the spiral pipe 3 are filled with fluid 4 (the arrow in the figure is the direction of fluid flow), and the fluid 4 contains solid particles 5 . Wherein, the mate...
PUM
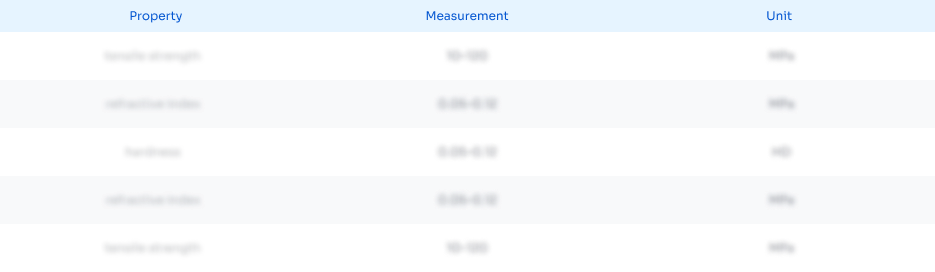
Abstract
Description
Claims
Application Information

- R&D Engineer
- R&D Manager
- IP Professional
- Industry Leading Data Capabilities
- Powerful AI technology
- Patent DNA Extraction
Browse by: Latest US Patents, China's latest patents, Technical Efficacy Thesaurus, Application Domain, Technology Topic, Popular Technical Reports.
© 2024 PatSnap. All rights reserved.Legal|Privacy policy|Modern Slavery Act Transparency Statement|Sitemap|About US| Contact US: help@patsnap.com