Production process of nano-copper latex pillow
A latex pillow and production process technology, applied in the field of nano-copper, can solve the problems of poor tear resistance, poor flame retardancy, poor support, etc., and achieve the effects of preventing tearing, good compatibility, high hardness and rigidity
- Summary
- Abstract
- Description
- Claims
- Application Information
AI Technical Summary
Problems solved by technology
Method used
Image
Examples
Embodiment Construction
[0025] The invention provides a technical solution: a production process of nano-copper latex pillows, comprising the following steps:
[0026] Step 1. Filter the collected resin through a filter device.
[0027] Step 2. Put the resin, zinc oxide and coagulant in step 1 into a mixing device for mixing.
[0028] Step 3, adding nanometer copper powder into the interior of the mixing device and mixing with the mixture in step 2.
[0029] Step 4. Add softener, high-viscosity plasticizer and rubber reinforcing agent to the inside of the mixing device and mix with the mixture in step 3.
[0030] Step 5, adding the halogenated flame retardant and high styrene rubber into the mixing device and mixing with the mixture in step 4.
[0031] Step 6. Pour the mixture in step 4 into a foaming mold for foaming, and then cook the foamed mixture through a cooking device.
[0032] Step 7. Clean the foamed mixture by cleaning equipment, and then manually cut the cleaned mixture to make nano-co...
PUM
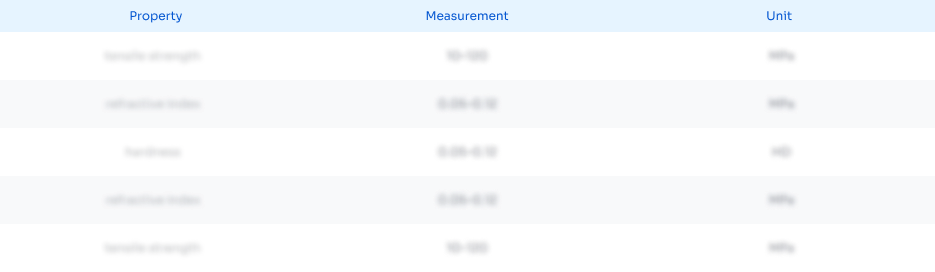
Abstract
Description
Claims
Application Information

- R&D
- Intellectual Property
- Life Sciences
- Materials
- Tech Scout
- Unparalleled Data Quality
- Higher Quality Content
- 60% Fewer Hallucinations
Browse by: Latest US Patents, China's latest patents, Technical Efficacy Thesaurus, Application Domain, Technology Topic, Popular Technical Reports.
© 2025 PatSnap. All rights reserved.Legal|Privacy policy|Modern Slavery Act Transparency Statement|Sitemap|About US| Contact US: help@patsnap.com