Torsional vibration damping system for hydrodynamic torque coupling device
A technology of torsional vibration and hydraulic torque, applied in vibration suppression adjustment, spring/shock absorber, mechanical equipment, etc., can solve problems such as large assembly tolerance, system cannot work stably, component manufacturing cost and assembly cost increase, etc. , to reduce design and production costs, facilitate compact setups, and increase the number of parts
- Summary
- Abstract
- Description
- Claims
- Application Information
AI Technical Summary
Problems solved by technology
Method used
Image
Examples
Embodiment Construction
[0044] In order to make the purpose, technical solution and advantages of the technical solution of the present invention clearer, the technical solutions of the embodiments of the present invention will be clearly and completely described below in conjunction with the drawings of specific embodiments of the present invention. The same reference numerals in the figures represent the same parts. It should be noted that the described embodiments are some of the embodiments of the present invention, but not all of the embodiments. Based on the described embodiments of the present invention, all other embodiments obtained by persons of ordinary skill in the art without creative efforts shall fall within the protection scope of the present invention.
[0045] Unless otherwise defined, the technical terms or scientific terms used herein shall have the usual meanings understood by those skilled in the art to which the present invention belongs. "First", "second" and similar words us...
PUM
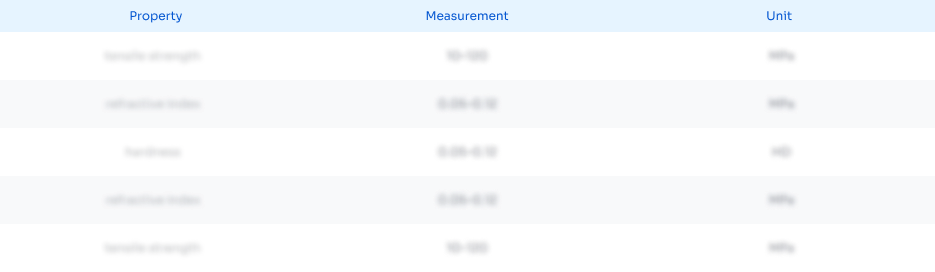
Abstract
Description
Claims
Application Information

- Generate Ideas
- Intellectual Property
- Life Sciences
- Materials
- Tech Scout
- Unparalleled Data Quality
- Higher Quality Content
- 60% Fewer Hallucinations
Browse by: Latest US Patents, China's latest patents, Technical Efficacy Thesaurus, Application Domain, Technology Topic, Popular Technical Reports.
© 2025 PatSnap. All rights reserved.Legal|Privacy policy|Modern Slavery Act Transparency Statement|Sitemap|About US| Contact US: help@patsnap.com