Manufacturing method of liquid crystal resin
A manufacturing method and technology of liquid crystallinity, which are applied in the field of manufacturing liquid crystal resins and can solve the problems of increased gas generation and the like
- Summary
- Abstract
- Description
- Claims
- Application Information
AI Technical Summary
Problems solved by technology
Method used
Image
Examples
Embodiment 1
[0080] After the following raw materials were charged into the polymerization vessel, the temperature of the reaction system was raised to 140°C, and the reaction was carried out at 140°C for 3 hours (acylation). Then, the temperature was further raised to 360° C. over 4.5 hours, and then the pressure was reduced to 10 Torr (ie, 1330 Pa) over 15 minutes, and polycondensation was performed while leaving acetic acid, excess acetic anhydride, and other low boiling points. The time from the start of decompression until the stirring torque reached the predetermined value was 20 minutes. After the stirring torque reached a predetermined value, nitrogen was introduced, the pressure was increased from the reduced pressure state to the normal pressure state, and the polymer was discharged from the lower part of the polymerization vessel. Then, the strands are pelletized to obtain liquid crystal resin pellets.
[0081] (raw material)
[0082] 4-Hydroxybenzoic acid (HBA): 184 g (60 mol%)...
Embodiment 2
[0089] Furthermore, liquid crystalline resin particles were obtained in the same manner as in Example 1 except that dimethylaminopyridine oxide was added. In addition, the usage-amount of dimethylaminopyridine oxide is as shown in Table 1.
Embodiment 3
[0091] Liquid-crystalline resin particles were obtained in the same manner as in Example 1, except that the B-O bond-containing compound was changed to 3,5-bis(trifluoromethyl)phenylboronic acid. In addition, Table 1 shows the usage-amount of 3,5-bis(trifluoromethyl)phenylboronic acid.
PUM
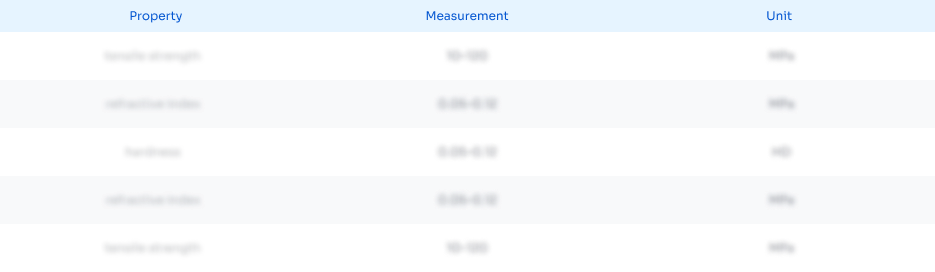
Abstract
Description
Claims
Application Information

- R&D Engineer
- R&D Manager
- IP Professional
- Industry Leading Data Capabilities
- Powerful AI technology
- Patent DNA Extraction
Browse by: Latest US Patents, China's latest patents, Technical Efficacy Thesaurus, Application Domain, Technology Topic, Popular Technical Reports.
© 2024 PatSnap. All rights reserved.Legal|Privacy policy|Modern Slavery Act Transparency Statement|Sitemap|About US| Contact US: help@patsnap.com