Milling parameter optimization method suitable for surface machining of thin-walled workpiece
A technology of surface processing and optimization methods, applied in metal processing equipment, design optimization/simulation, milling machine equipment, etc., can solve the problems of reduced reliability of parts, unreliable experience, shortened service life, etc., to reduce tool wear, reduce The number of experiments, the optimal combination of precise effects
- Summary
- Abstract
- Description
- Claims
- Application Information
AI Technical Summary
Problems solved by technology
Method used
Image
Examples
Embodiment Construction
[0021] Such as figure 1 As shown, a method for optimizing milling parameters suitable for surface processing of thin-walled parts provided in this embodiment includes the following steps:
[0022] (1) Select the milling parameters and evaluation factors to be optimized according to the material of the thin-walled part, wherein the milling parameters include milling width, milling depth, spindle speed and feed rate, and the evaluation factors include surface roughness and residual stress ;
[0023] (2) According to the milling parameters selected in step (1), the face-centered cubic design method is used to determine the level of each milling parameter, and four factors and three levels are established;
[0024] (3) Carry out the milling simulation experiment according to the four-factor three-level table described in step (2) to obtain the surface roughness and residual stress on the surface of the thin-walled part;
[0025] (4) Construct a mathematical model between the eva...
PUM
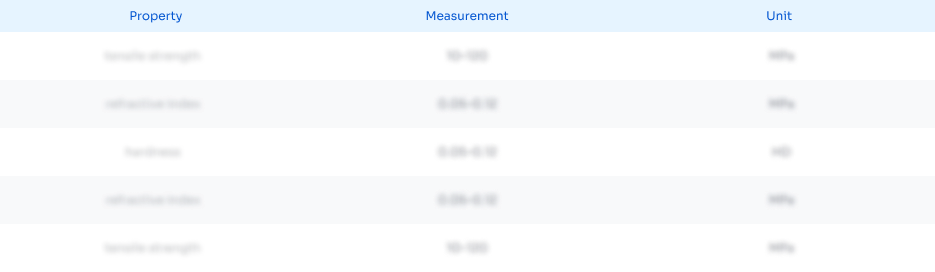
Abstract
Description
Claims
Application Information

- R&D
- Intellectual Property
- Life Sciences
- Materials
- Tech Scout
- Unparalleled Data Quality
- Higher Quality Content
- 60% Fewer Hallucinations
Browse by: Latest US Patents, China's latest patents, Technical Efficacy Thesaurus, Application Domain, Technology Topic, Popular Technical Reports.
© 2025 PatSnap. All rights reserved.Legal|Privacy policy|Modern Slavery Act Transparency Statement|Sitemap|About US| Contact US: help@patsnap.com