A kind of master batch for reducing foaming temperature and its application
A foaming temperature and masterbatch technology, applied in the field of PVB foaming product production, can solve the problems of raw material volatilization, raw material consumption and waste, poor foaming effect, etc., achieve stable and stable foaming ratio, reduce foaming temperature, and ensure foaming bubble effect effect
- Summary
- Abstract
- Description
- Claims
- Application Information
AI Technical Summary
Problems solved by technology
Method used
Image
Examples
Embodiment 1
[0028] Embodiment 1: A master batch for reducing foaming temperature, which is composed of the following raw materials by weight percentage: 8% of glycerol, 12% of urea, 55% of zinc cyanurate, and 25% of zinc glycerol.
[0029] The preparation method includes the following steps: mixing glycerol, urea, zinc cyanurate and zinc glycerol according to the above weight percentages in a high-speed mixer with high-speed stirring, the stirring speed of the high-speed mixer is 5000r / min, and the stirring time is 125 rpm; After ℃, extrusion and granulation are carried out to prepare master batches with a particle size of 0.5 cm.
Embodiment 2
[0030] Embodiment 2: A master batch for reducing foaming temperature, which is composed of the following raw materials by weight: 12% of glycerol, 18% of urea, 50% of zinc cyanurate, and 20% of zinc glycerol.
[0031] The preparation method includes the following steps: mixing glycerol, urea, zinc cyanurate and zinc glycerol according to the above weight percentages in a high-speed mixer at a high speed, the mixing speed of the high-speed mixer is 4000r / min, and the stirring time is 120 r / min; then the temperature is raised to 120 After ℃, extrusion and granulation are carried out to prepare master batches with a particle size of 0.5 cm.
Embodiment 3
[0032] Embodiment 3: a master batch for reducing foaming temperature, which is composed of the following raw materials by weight: 10% of glycerol, 15% of urea, 52% of zinc cyanurate, and 23% of zinc glycerol.
[0033] The preparation method includes the following steps: mixing glycerol, urea, zinc cyanurate and zinc glycerol according to the above weight percentages in a high-speed mixer with a high-speed stirring speed of 4500 r / min and a stirring time of 122 After ℃, extrusion and granulation are carried out to prepare master batches with a particle size of 0.5 cm.
PUM
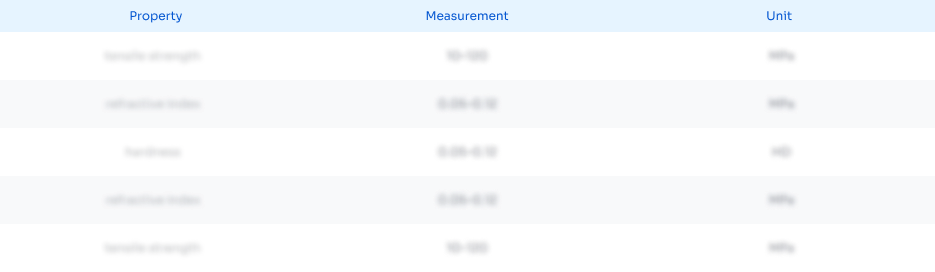
Abstract
Description
Claims
Application Information

- Generate Ideas
- Intellectual Property
- Life Sciences
- Materials
- Tech Scout
- Unparalleled Data Quality
- Higher Quality Content
- 60% Fewer Hallucinations
Browse by: Latest US Patents, China's latest patents, Technical Efficacy Thesaurus, Application Domain, Technology Topic, Popular Technical Reports.
© 2025 PatSnap. All rights reserved.Legal|Privacy policy|Modern Slavery Act Transparency Statement|Sitemap|About US| Contact US: help@patsnap.com