Spatially deployable prism unit for in-orbit assembly
A space and prism technology, applied in the field of space deployable prism units, can solve problems such as the deployment failure of the ring truss deployable antenna, the inability to realize the space detection task, and the failure to meet the rigidity required for use, so as to achieve good symmetry and load-bearing performance Good, large fold-to-expand ratio
- Summary
- Abstract
- Description
- Claims
- Application Information
AI Technical Summary
Problems solved by technology
Method used
Image
Examples
Embodiment Construction
[0024] see Figure 1-Figure 5 As shown, a space-deployable prism unit for on-rail assembly includes a synchronous mechanism 1, an inner cross bar 2, an outer vertical bar 3, and a central vertical bar 4; multiple synchronous mechanisms 1 are connected end to end to form two upper and lower rings , the adjacent synchronization mechanism 1 in the same ring is folded and limited by the connected vortex spring hinge 5, and the two rings are connected by the outer vertical rod 3 connected with the synchronization mechanism 1 to form a regular hexagonal prism unit, and the center of the regular hexagonal prism unit is set There is a central vertical bar 4, and the central vertical bar 4 is rotationally connected with the synchronous mechanism 1 through the foldable inner horizontal bar 2 to form a regular hexagonal prism folding unit. The three synchronous mechanisms 1 arranged alternately in the upper ring are respectively connected to the lower ring The two synchronous mechanisms ...
PUM
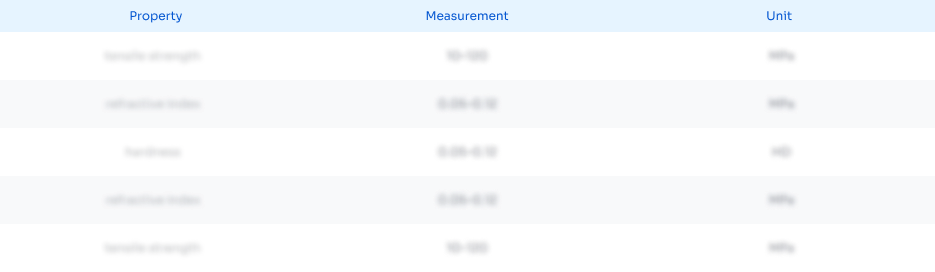
Abstract
Description
Claims
Application Information

- R&D
- Intellectual Property
- Life Sciences
- Materials
- Tech Scout
- Unparalleled Data Quality
- Higher Quality Content
- 60% Fewer Hallucinations
Browse by: Latest US Patents, China's latest patents, Technical Efficacy Thesaurus, Application Domain, Technology Topic, Popular Technical Reports.
© 2025 PatSnap. All rights reserved.Legal|Privacy policy|Modern Slavery Act Transparency Statement|Sitemap|About US| Contact US: help@patsnap.com