Fabric conveying and processing device for chemical fiber quilt production
A processing device and fabric technology, which is applied in the cutting and processing of chemical fiber quilt fabrics, and in the field of fabric transmission and processing devices produced by chemical fiber quilts, which can solve the problem of unwinding and conveying of difficult fabrics, skewed and wrinkled fabrics, and affecting the quality of subsequent fabric cutting and processing processes and other issues to achieve the effect of reasonable structural design
- Summary
- Abstract
- Description
- Claims
- Application Information
AI Technical Summary
Problems solved by technology
Method used
Image
Examples
Embodiment Construction
[0018] In order to further describe the present invention, a specific implementation of a fabric conveying and processing device for chemical fiber production is further described below in conjunction with the accompanying drawings. The following examples are explanations of the present invention and the present invention is not limited to the following examples.
[0019] Such as figure 1 As shown, the present invention is a fabric conveying and processing device for chemical fiber production, comprising a fabric processing support 1, a fabric conveying mechanism 2, a feed conveying support 3, a fabric pulling chain 4, a fabric pulling motor 5, a translational reciprocating pulling Plate 6, connecting rod reciprocating support 7, fabric cutting mechanism 8 and fabric guiding mechanism 9, such as figure 2 As shown, the fabric conveying mechanism 2 of the present invention comprises a fabric unwinding support 10, a fabric unwinding roller 11, a fabric conveying turntable 12, an...
PUM
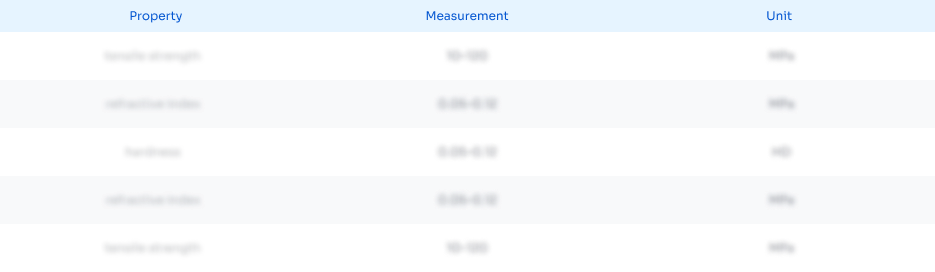
Abstract
Description
Claims
Application Information

- Generate Ideas
- Intellectual Property
- Life Sciences
- Materials
- Tech Scout
- Unparalleled Data Quality
- Higher Quality Content
- 60% Fewer Hallucinations
Browse by: Latest US Patents, China's latest patents, Technical Efficacy Thesaurus, Application Domain, Technology Topic, Popular Technical Reports.
© 2025 PatSnap. All rights reserved.Legal|Privacy policy|Modern Slavery Act Transparency Statement|Sitemap|About US| Contact US: help@patsnap.com