micro LED wafer structure and its preparation method
An LED structure and wafer technology, applied in semiconductor devices, electrical components, circuits, etc., can solve problems such as large dislocations in the epitaxial layer of LED chips, improve luminous efficiency, parameter consistency, good contact effect, and reduce the number of strings. light effect
- Summary
- Abstract
- Description
- Claims
- Application Information
AI Technical Summary
Problems solved by technology
Method used
Image
Examples
Embodiment 1
[0051] like Figure 1 to Figure 6 As shown, this embodiment provides a method for preparing a Micro LED wafer structure, and the preparation method includes steps:
[0052] like figure 1 As shown, step 1) and step 2) are first performed to provide a single crystal substrate 101, 201, the single crystal substrate 101, 201 includes opposite first and second surfaces, on the single crystal substrate An LED structure layer is formed on the first surface of 101, 201, and a plurality of Micro LED arrays are prepared on the single crystal substrate 101, 201 based on the LED structure layer.
[0053] The single crystal substrates 101, 201 may be compound single crystal substrates of Group III and Group V. In this embodiment, the single crystal substrates 101, 201 are selected as GaN single crystal substrates. The present invention uses single crystal substrates 101, 201 (such as single crystal GaN substrates) to grow each layer of the chip, which greatly reduces the dislocation dens...
Embodiment 2
[0076] like Figure 7 ~ Figure 9 As shown, this embodiment also provides a Micro LED wafer structure and its preparation method, the basic steps and basic structure of which are similar to those of Embodiment 1, wherein the difference from Embodiment 1 is that the Micro LED array does not The second conductive layer 109 needs to be prepared in the Micro LED chip. The N electrode 116 (common cathode electrode) of the Micro LED array is formed at the common cathode path and between the Micro LED chips. On the one hand, the common cathode electrode is connected to the driver The circuit connection, on the other hand, reduces the voltage drop generated by the common cathode path, so that the voltage of each Micro LED chip is consistent when it is working. Based on this, the area of the Micro LED chip can be greatly saved, thereby greatly improving the luminescence per unit area of the Micro LED chip. strength.
[0077] As an example, the common cathode electrode may be in the...
PUM
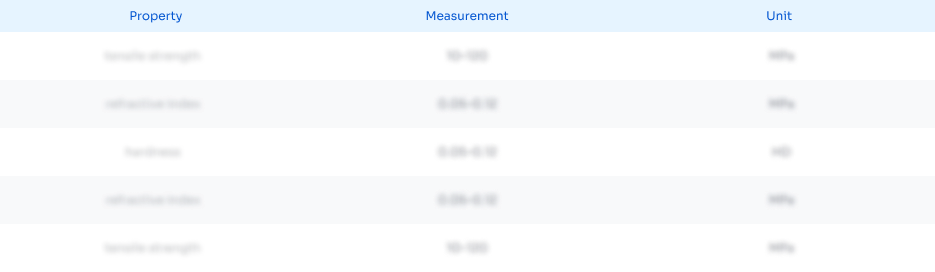
Abstract
Description
Claims
Application Information

- R&D
- Intellectual Property
- Life Sciences
- Materials
- Tech Scout
- Unparalleled Data Quality
- Higher Quality Content
- 60% Fewer Hallucinations
Browse by: Latest US Patents, China's latest patents, Technical Efficacy Thesaurus, Application Domain, Technology Topic, Popular Technical Reports.
© 2025 PatSnap. All rights reserved.Legal|Privacy policy|Modern Slavery Act Transparency Statement|Sitemap|About US| Contact US: help@patsnap.com