A wear-resistant copper-alumina composite material and its preparation method
A composite material, copper alumina technology, applied in the field of copper alloy, can solve the problems of poor wear resistance, etc., and achieve the effect of good wear resistance, high hardness and compact structure
- Summary
- Abstract
- Description
- Claims
- Application Information
AI Technical Summary
Problems solved by technology
Method used
Examples
preparation example Construction
[0028] A method for preparing a wear-resistant copper-alumina composite material, comprising the following steps:
[0029] Step 1. Preparation of alumina particles
[0030] Step 1.1, fully dissolve aluminum sulfate hydrate in deionized water, and obtain 0.1-0.2mol / L aluminum sulfate solution after ultrasonic vibration;
[0031] Step 1.2, adding 2-3 wt% polyethylene glycol and 0.5-0.8 mol / L ammonia solution to the aluminum sulfate solution, mixing fully and stirring evenly to obtain a solution;
[0032] Step 1.3, transfer the solution to the reaction kettle, and place the reaction kettle in an electric blast drying oven to heat at 120-150°C and keep it warm for 12-15 hours;
[0033] Step 1.4. Take out the reaction kettle and cool it down to room temperature naturally, wash the precipitate in the reaction kettle with deionized water and absolute ethanol, put it in a vacuum oven at 80-90°C for 15-20 minutes to constant weight, grind it thoroughly and dry it again , to obtain al...
Embodiment 1
[0044] Step 1. Fully dissolve aluminum sulfate hydrate in deionized water, and obtain a 0.1mol / L aluminum sulfate solution after ultrasonic vibration; add 2wt% polyethylene glycol and 0.5mol / L ammonia solution to the aluminum sulfate solution, mix well and stir Evenly, the solution was obtained; the solution was transferred to the reaction kettle, and the reaction kettle was heated at 120°C in an electric blast drying oven, and kept for 12 hours; the reaction kettle was taken out and cooled to room temperature naturally, and the precipitate in the reaction kettle was treated with deionized water Wash with absolute ethanol, dry in a vacuum oven at 80° C. for 15 minutes to constant weight, fully grind and dry again to obtain alumina particles.
[0045]Step 2. Dissolve aluminum chloride hydrate in a mixed solution of absolute ethanol and DMF to obtain a mixed solution with a concentration of aluminum chloride of 0.65 mol / L, and the volume ratio of absolute ethanol and DMF is 1:1.1...
Embodiment 2
[0050] Step 1. Fully dissolve aluminum sulfate hydrate in deionized water, obtain 0.15mol / L aluminum sulfate solution after ultrasonic vibration; add 2.5wt% polyethylene glycol and 0.6mol / L ammonia solution to the aluminum sulfate solution, mix thoroughly and Stir evenly to obtain a solution; transfer the solution to a reaction kettle, and place the reaction kettle in an electric blast drying oven to heat at 140°C and keep it warm for 14 hours; take out the reaction kettle and cool it to room temperature naturally, and deionize the precipitate in the reaction kettle Wash with water and absolute ethanol, dry in a vacuum oven at 80°C for 18 minutes to constant weight, grind thoroughly and dry again to obtain alumina particles.
[0051] Step 2. Dissolve aluminum chloride hydrate in the mixed solution of absolute ethanol and DMF to obtain a mixed solution with a concentration of aluminum chloride of 0.72mol / L, and the volume ratio of absolute ethanol and DMF is 1:1.2; add 12wt% PV...
PUM
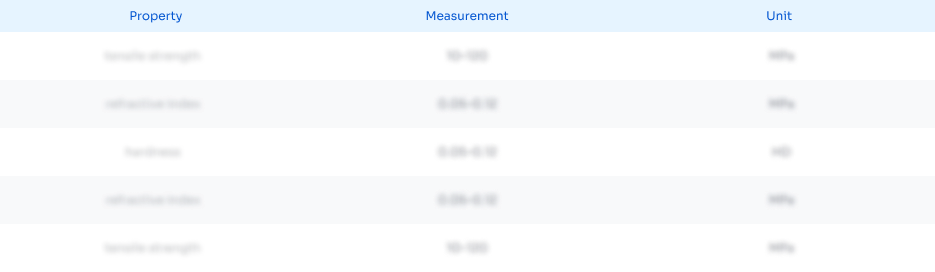
Abstract
Description
Claims
Application Information

- Generate Ideas
- Intellectual Property
- Life Sciences
- Materials
- Tech Scout
- Unparalleled Data Quality
- Higher Quality Content
- 60% Fewer Hallucinations
Browse by: Latest US Patents, China's latest patents, Technical Efficacy Thesaurus, Application Domain, Technology Topic, Popular Technical Reports.
© 2025 PatSnap. All rights reserved.Legal|Privacy policy|Modern Slavery Act Transparency Statement|Sitemap|About US| Contact US: help@patsnap.com