Self-adaptive coal mining machine follow-up tracking multi-camera video splicing method
A follow-up tracking, multi-camera technology, applied in image enhancement, image analysis, image data processing, etc., can solve the problem that dynamic large-scale target follow-up monitoring has not been fully studied, video stitching results are blurred and distorted, and limit the vertical expansion of monitoring range. And other issues
- Summary
- Abstract
- Description
- Claims
- Application Information
AI Technical Summary
Problems solved by technology
Method used
Image
Examples
Embodiment Construction
[0088] The structure and performance of the present invention will be further described below with reference to the accompanying drawings.
[0089] like Figure 1-12 As shown, the adaptive shearer tracking multi-camera video stitching method includes the following steps: manually marking the ROI (using a colored fluorescent band) at the central part of the shearer as the positioning anchor point of the camera calibration algorithm. The color component feature extraction algorithm is used to retrieve the ROI anchor points in the images collected by each camera, and at a certain algorithm time interval t q The ROI anchor point polling retrieval is performed on the video data of each camera in the order from left to right. If an anchor point is retrieved by one or several cameras, the subsequent cameras will stop retrieving. Then, according to the mapping relationship between the pixel coordinates and the real coordinates in the camera calibration, the camera group to be called ...
PUM
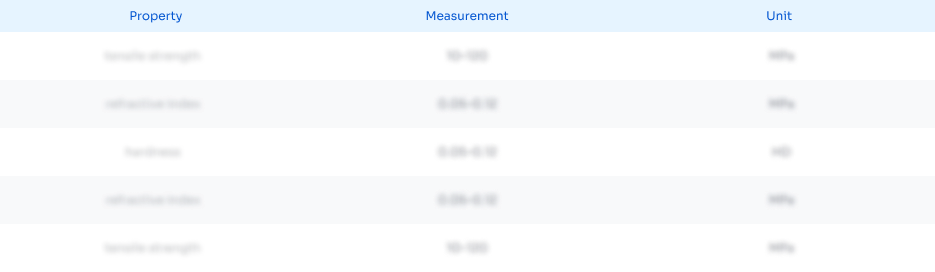
Abstract
Description
Claims
Application Information

- R&D
- Intellectual Property
- Life Sciences
- Materials
- Tech Scout
- Unparalleled Data Quality
- Higher Quality Content
- 60% Fewer Hallucinations
Browse by: Latest US Patents, China's latest patents, Technical Efficacy Thesaurus, Application Domain, Technology Topic, Popular Technical Reports.
© 2025 PatSnap. All rights reserved.Legal|Privacy policy|Modern Slavery Act Transparency Statement|Sitemap|About US| Contact US: help@patsnap.com