A Turbine Blade Vibration Fatigue Simulator and Its Design Method
A turbine blade and vibration fatigue technology is applied in the field of turbine blade vibration fatigue simulation parts and its design.
- Summary
- Abstract
- Description
- Claims
- Application Information
AI Technical Summary
Problems solved by technology
Method used
Image
Examples
Embodiment Construction
[0042] It should be noted that, in the case of no conflict, the embodiments in the present application and the features in the embodiments can be combined with each other. The present invention will be described in detail below with reference to the accompanying drawings and examples.
[0043] like figure 1 and figure 2 As shown, a turbine blade vibration fatigue simulation, including:
[0044] Clamping section 1, used for fixing on the test bench during the test;
[0045] The airfoil section 2 is fixed on the clamping section 1 and has a symmetrical cross-sectional shape. The vibration stress ratio of the blade back root 6 and the leading edge root 7 in the root of the airfoil section 2 is the same as that of the designed turbine blade model. The vibration stress ratio of the blade basin / back dangerous point in the vibration modal analysis is equal, and the length L of the airfoil section 2 makes the first-order bending natural frequency of the turbine blade vibration fat...
PUM
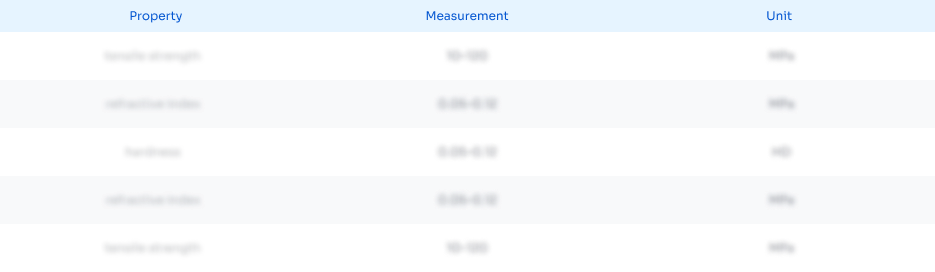
Abstract
Description
Claims
Application Information

- R&D Engineer
- R&D Manager
- IP Professional
- Industry Leading Data Capabilities
- Powerful AI technology
- Patent DNA Extraction
Browse by: Latest US Patents, China's latest patents, Technical Efficacy Thesaurus, Application Domain, Technology Topic, Popular Technical Reports.
© 2024 PatSnap. All rights reserved.Legal|Privacy policy|Modern Slavery Act Transparency Statement|Sitemap|About US| Contact US: help@patsnap.com