A Repair and Reinforcement Structure of Complicated Space Steel Tube Structure
A technology for reinforcing structures and steel pipes, applied in the direction of pipe elements, pipes/pipe joints/pipes, mechanical equipment, etc., can solve the problems of lack of research and design, late start and other problems, to achieve convenient cutting and wrapping, saving time, and convenient construction Effect
- Summary
- Abstract
- Description
- Claims
- Application Information
AI Technical Summary
Problems solved by technology
Method used
Image
Examples
Embodiment 1
[0082] see figure 1 , figure 2 , Figure 5 , Image 6 , Figure 8 As shown, this embodiment is a repair and reinforcement structure of a complex space steel pipe structure, including a steel pipe node main pipe 1 and three steel pipe node branch pipes 2, and the three steel pipe node branch pipes 2 are respectively oblique to the steel pipe node main pipe 1 and are all column-shaped pipes. , the steel pipe node branch pipe 2 includes two first steel pipe node branch pipes 2, the first steel pipe node branch pipe 2 and the steel pipe node main pipe 1 form a K-shaped pipe, and the remaining steel pipe node branch pipe 2 is the second steel pipe node branch pipe 3, the second steel pipe node branch pipe 3 The branch pipe 3 and the steel pipe node main pipe 1 form a Y-shaped pipe, and the orthographic projection of the root of the second steel pipe node branch pipe 3 is located between the two first steel pipe node branch pipes 2;
[0083] Several layers of carbon fiber reinf...
Embodiment 2
[0111] see figure 1 , image 3 , Figure 4 , Figure 5 , Image 6 , Figure 8As shown, this embodiment is a repair and reinforcement structure of a complex space steel pipe structure, including a steel pipe node main pipe 1 and three steel pipe node branch pipes 2, and the three steel pipe node branch pipes 2 are respectively oblique to the steel pipe node main pipe 1 and are all column-shaped pipes. , the steel pipe node branch pipe 2 includes two first steel pipe node branch pipes 2, the first steel pipe node branch pipe 2 and the steel pipe node main pipe 1 form a K-shaped pipe, and the remaining steel pipe node branch pipe 2 is the second steel pipe node branch pipe 3, the second steel pipe node branch pipe 3 The branch pipe 3 and the steel pipe node main pipe 1 form a Y-shaped pipe, and the orthographic projection of the root of the second steel pipe node branch pipe 3 is located between the two first steel pipe node branch pipes 2;
[0112] Several layers of carbon ...
Embodiment 3
[0141] The difference from Embodiment 1 and Embodiment 2 is that if the second steel pipe node branch pipe 3 is relatively thin, only one piece of rectangular branch pipe carbon fiber cloth for each layer of the second branch pipe carbon fiber cloth 502 is required, such as Figure 7 shown, and there is only one overlap area.
PUM
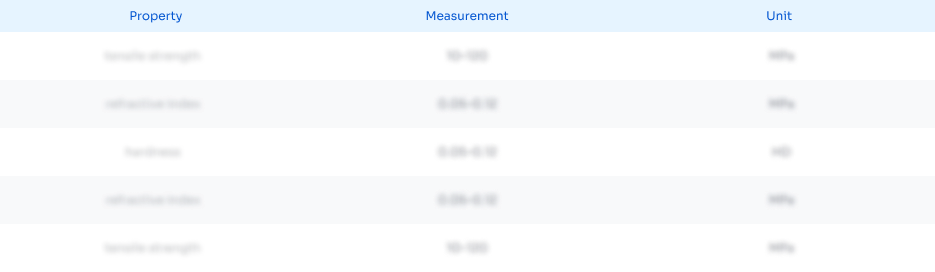
Abstract
Description
Claims
Application Information

- R&D
- Intellectual Property
- Life Sciences
- Materials
- Tech Scout
- Unparalleled Data Quality
- Higher Quality Content
- 60% Fewer Hallucinations
Browse by: Latest US Patents, China's latest patents, Technical Efficacy Thesaurus, Application Domain, Technology Topic, Popular Technical Reports.
© 2025 PatSnap. All rights reserved.Legal|Privacy policy|Modern Slavery Act Transparency Statement|Sitemap|About US| Contact US: help@patsnap.com