Process for synthesizing nitro diether by adopting narrow-distance parallel plate reactor
A parallel plate, nitro bis-ether technology, applied in the direction of ester reaction to prepare ether, chemical/physical/physical chemical reactor details, chemical/physical/physical chemical fixed reactor, etc., can solve the problem of high energy consumption and cost problems, achieving shorter reaction times, lower risk, and lower risk of explosion
- Summary
- Abstract
- Description
- Claims
- Application Information
AI Technical Summary
Problems solved by technology
Method used
Image
Examples
Embodiment 1
[0040] Such as figure 1 Shown, a kind of technique that adopts narrow-distance parallel plate reactor to synthesize nitrobisethers specifically comprises the following steps:
[0041] 1) Preparation of 1,3-bis[2-chloro-4-(trifluoromethyl)phenoxy]benzene and solvent mixed solution:
[0042] 400kg of solid 1,3-bis[2-chloro-4-(trifluoromethyl)phenoxy]benzene is dropped into a stainless steel mixing kettle with heating and stirring, and then by mass ratio (solvent: 1,3-bis[ 2-Chloro-4-(trifluoromethyl)phenoxy]benzene) 3:1 transport the dichloroethane from the dichloroethane storage tank to the stainless steel mixing kettle through the pump, start stirring and heating after the solvent is added, After the solid material is completely dissolved, the mixed solution is pumped to the mixed solution raw material tank through the mixing tank;
[0043] 2) Preparation of mixed acid:
[0044] The fuming nitric acid with a mass concentration of 98% is transported from the nitric acid stor...
Embodiment 2
[0054] A process for synthesizing nitrobisethers using narrow-distance parallel plate reactors, specifically comprising the following steps:
[0055] 1) Preparation of 1,3-bis[2-chloro-4-(trifluoromethyl)phenoxy]benzene and solvent mixed solution:
[0056] 400kg of solid 1,3-bis[2-chloro-4-(trifluoromethyl)phenoxy]benzene is dropped into a stainless steel mixing kettle with heating and stirring, and then by mass ratio (solvent: 1,3-bis[ 2-Chloro-4-(trifluoromethyl)phenoxy]benzene) 3:1 Transport the petroleum ether from the petroleum ether storage tank to the stainless steel mixing kettle through the pump, start stirring and heating after the solvent is added, and wait until the solid material is completely After dissolving, the mixed solution is pumped to the mixed solution raw material tank through the mixing tank;
[0057] 2) Preparation of mixed acid:
[0058] The nitric acid with a mass concentration of 68% is transported from the nitric acid storage tank to the static m...
Embodiment 3
[0068] A process for synthesizing nitrobisethers using narrow-distance parallel plate reactors, comprising the following steps:
[0069] 1) 1) Preparation of 1,3-bis[2-chloro-4-(trifluoromethyl)phenoxy]benzene and solvent mixed solution:
[0070] 400kg of solid 1,3-bis[2-chloro-4-(trifluoromethyl)phenoxy]benzene is dropped into a stainless steel mixing kettle with heating and stirring, and then by mass ratio (solvent: 1,3-bis[ 2-Chloro-4-(trifluoromethyl)phenoxy]benzene) 3:1 Send equal volumes of dichloroethane and petroleum ether from the dichloroethane storage tank and petroleum ether storage tank to the stainless steel mixing tank respectively. After the addition of the solvent, start stirring and heating. After the solid material is completely dissolved, the mixed solution is pumped to the mixed solution raw material tank through the mixing kettle;
[0071] 2) Preparation of mixed acid
[0072] The fuming nitric acid with a mass concentration of 75% is transported from t...
PUM
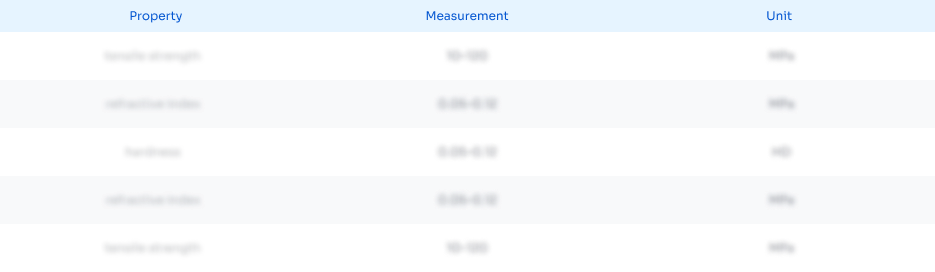
Abstract
Description
Claims
Application Information

- R&D
- Intellectual Property
- Life Sciences
- Materials
- Tech Scout
- Unparalleled Data Quality
- Higher Quality Content
- 60% Fewer Hallucinations
Browse by: Latest US Patents, China's latest patents, Technical Efficacy Thesaurus, Application Domain, Technology Topic, Popular Technical Reports.
© 2025 PatSnap. All rights reserved.Legal|Privacy policy|Modern Slavery Act Transparency Statement|Sitemap|About US| Contact US: help@patsnap.com