Full-automatic filter plate production equipment and process
A production equipment, fully automatic technology, used in metal processing, other household appliances, household components, etc., to achieve the effect of improving accuracy, ensuring molding quality, and preventing falling
- Summary
- Abstract
- Description
- Claims
- Application Information
AI Technical Summary
Problems solved by technology
Method used
Image
Examples
Embodiment 1
[0071] Such as figure 1 and 2 As shown, a filter plate automatic production equipment and its process are used for forming a filter plate 10. The filter plate 10 includes a filter plate main body 101 and a filter hole 102. The side of the filter plate main body 101 Several filter holes 102 are provided, and the two ends of the filter plate main body 101 are provided with a filter press section 103, and the filter holes 102 and the filter press section 103 are communicated with each other through a flow channel 104, and the equipment includes:
[0072] The first conveying mechanism 1, the first conveying mechanism 1 is provided with a first track 11 along its conveying direction;
[0073] The carrying mechanism 2, the carrying mechanism 2 is arranged in an array along the conveying direction of the first conveying mechanism 1, the carrying mechanism 2 includes a carrying frame 21 and a molding assembly 22, and the carrying frame 21 is conveyed along the first track 11 The fil...
Embodiment 2
[0107] A fully automatic production process for filter plates, which comprises the following steps;
[0108] Step 1: Feeding process, the first conveying mechanism 1 conveys the carrying frame 21 to the molding station at intervals along the conveying direction of the first rail 11, and the second conveying mechanism 4 is pushed by the third cylinder 42 to convey the raw material 9 at intervals to the molding station In the bearing frame 21 on the position;
[0109] Step 2: Pressing process, the upper pressing plate 32 and the lower pressing plate 34 work together to press the raw material 9 in the bearing frame 21 on the pressing station into a filter press plate 10;
[0110] Step 3: the filter hole forming process, the first conveying mechanism 1 transports the carrying frame 21 for transfer, during the transfer process, the second rail 54 is set against the first bump 2212, and the second rail 54 drives the sleeve 221 to slide outward , at the same time, the third track 55...
PUM
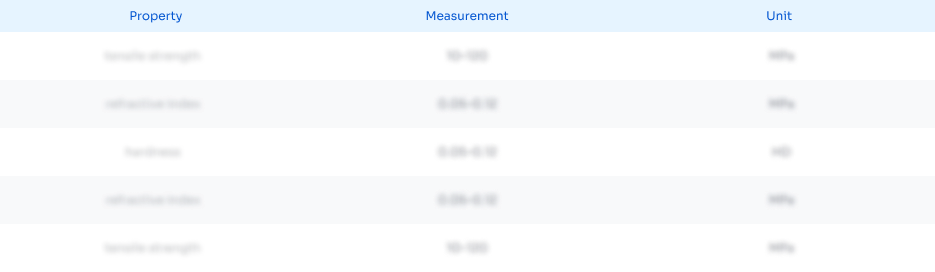
Abstract
Description
Claims
Application Information

- R&D
- Intellectual Property
- Life Sciences
- Materials
- Tech Scout
- Unparalleled Data Quality
- Higher Quality Content
- 60% Fewer Hallucinations
Browse by: Latest US Patents, China's latest patents, Technical Efficacy Thesaurus, Application Domain, Technology Topic, Popular Technical Reports.
© 2025 PatSnap. All rights reserved.Legal|Privacy policy|Modern Slavery Act Transparency Statement|Sitemap|About US| Contact US: help@patsnap.com