Distributed optical fiber strain sensing calibration system and method
A distributed optical fiber and calibration system technology, which is applied in the field of distributed optical fiber strain sensing calibration system, can solve the problems of difficult linear expansion and micro-strain control, which is not conducive to mass production efficiency, difficult and time-consuming winding of optical fibers, etc., and achieves benefits Batch production, high overall stability and easy operation
- Summary
- Abstract
- Description
- Claims
- Application Information
AI Technical Summary
Problems solved by technology
Method used
Image
Examples
Embodiment approach
[0037] Such as Figure 1-2 As shown, an embodiment of one aspect of the present invention is a distributed optical fiber strain sensing calibration system, including: a base 1, a slide rail 2, a sliding block 3, a transmission seat 4, a power device 7, a displacement transmission device 5 and a measuring device 6. A slide rail 2 and a transmission seat 4 are fixedly installed on the base 1, and a slide block 3 that can move along the slide rail 2 is provided at one end of the slide rail 2, and the slide block 3 clamps the fiber 10 to be tested. One end, the other end of the optical fiber 10 to be tested is clamped at the fixed end 9 of the optical fiber. The fixed end 9 of the optical fiber is directly installed on a movable solid structure. There are multiple movable brackets between the fixed end 9 of the optical fiber and the base 1. 8. The movable bracket 8 is used to support the optical fiber 10 to be tested, the sliding block 3 is connected to the displacement transmissi...
PUM
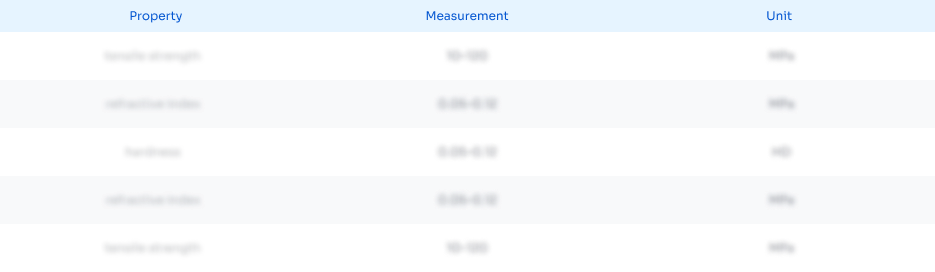
Abstract
Description
Claims
Application Information

- R&D
- Intellectual Property
- Life Sciences
- Materials
- Tech Scout
- Unparalleled Data Quality
- Higher Quality Content
- 60% Fewer Hallucinations
Browse by: Latest US Patents, China's latest patents, Technical Efficacy Thesaurus, Application Domain, Technology Topic, Popular Technical Reports.
© 2025 PatSnap. All rights reserved.Legal|Privacy policy|Modern Slavery Act Transparency Statement|Sitemap|About US| Contact US: help@patsnap.com