Electrophoretic coating system
A coating system and electrophoretic coating technology, applied in the direction of electrophoretic coating, electrolytic coating, coating, etc., can solve the problems that affect the efficiency and effect of electrophoretic coating of workpieces, insufficient mechanization degree, and insufficient compact structure, etc., to improve market competition Power, safe and convenient to use, and the effect of improving efficiency
- Summary
- Abstract
- Description
- Claims
- Application Information
AI Technical Summary
Problems solved by technology
Method used
Image
Examples
Embodiment
[0047] Example: such as Figure 1-7 An electrophoretic coating coating system shown includes a derusting device 100 and an electrophoretic device 200. After the workpiece is degreased, derusted, phosphating and passivated, it enters the electrophoretic tank 3 of the electrophoretic device 200 for electrophoretic coating , wherein the rust removal of the workpiece is carried out in the rust removal device 100, the rust removal device 100 includes a mounting rod 101, the lower end of the mounting rod 101 is fixed with a pneumatic telescopic rod 102, and the lower end of the rod body of the pneumatic telescopic rod 102 is fixedly connected with a rotating motor 103, and the rotating motor The rotating shaft 104 extends into the metal mesh cylinder 105, and the center of the bottom plate of the metal mesh cylinder 105 is fixed with a positioning convex edge 107 through a connecting rod 106. The connecting rod 106 and the positioning convex edge 107 are inserted into the connecting ...
PUM
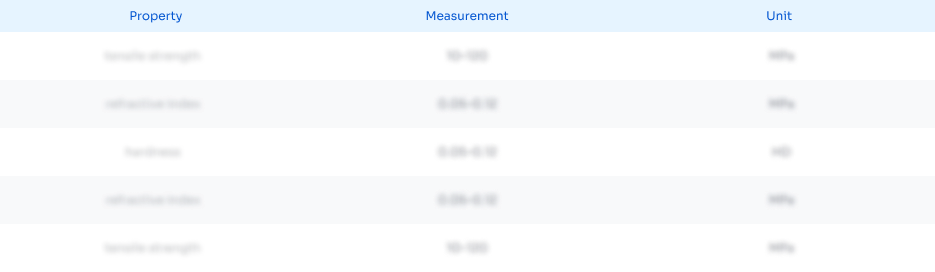
Abstract
Description
Claims
Application Information

- R&D Engineer
- R&D Manager
- IP Professional
- Industry Leading Data Capabilities
- Powerful AI technology
- Patent DNA Extraction
Browse by: Latest US Patents, China's latest patents, Technical Efficacy Thesaurus, Application Domain, Technology Topic, Popular Technical Reports.
© 2024 PatSnap. All rights reserved.Legal|Privacy policy|Modern Slavery Act Transparency Statement|Sitemap|About US| Contact US: help@patsnap.com