A passive wireless robotic gripper based on a mechanical metamaterial structure
A passive wireless and metamaterial technology, applied in manipulators, micro manipulators, manufacturing tools, etc., to achieve high precision, small size, and strong reliability
- Summary
- Abstract
- Description
- Claims
- Application Information
AI Technical Summary
Problems solved by technology
Method used
Image
Examples
Embodiment Construction
[0019] The present invention will be further described below in conjunction with the accompanying drawings.
[0020] see figure 1 , figure 2 and image 3 , the present invention provides a passive wireless machine gripper based on a mechanical metamaterial structure, comprising a graphene oxide layer 1 of a mechanical metamaterial structure, a graphene layer 2 of a mechanical metamaterial structure, a capacitor upper plate 3, a dielectric Layer 4, capacitor lower plate 5, anchor region 6, planar inductor 7, through hole 8, substrate 9; the graphene layer 2 of the mechanical metamaterial structure is located below the graphene oxide layer 1 of the mechanical metamaterial structure to form a double-layer mechanical superstructure Material structure, the double-layer mechanical metamaterial structure is located on the front of the substrate 9, and the center of the mechanical metamaterial structure is a pressure-sensitive capacitor, which consists of the capacitor upper plate ...
PUM
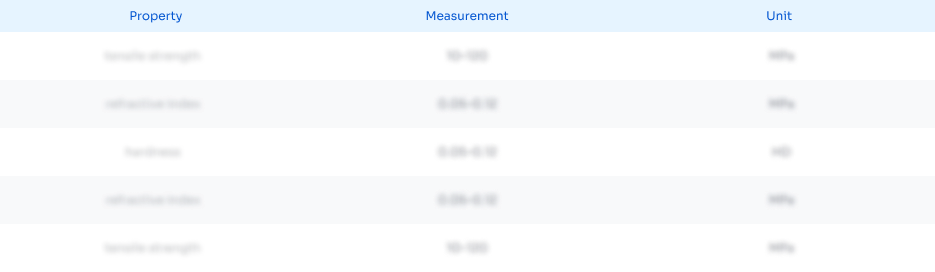
Abstract
Description
Claims
Application Information

- R&D
- Intellectual Property
- Life Sciences
- Materials
- Tech Scout
- Unparalleled Data Quality
- Higher Quality Content
- 60% Fewer Hallucinations
Browse by: Latest US Patents, China's latest patents, Technical Efficacy Thesaurus, Application Domain, Technology Topic, Popular Technical Reports.
© 2025 PatSnap. All rights reserved.Legal|Privacy policy|Modern Slavery Act Transparency Statement|Sitemap|About US| Contact US: help@patsnap.com