Floating main shaft
A spindle and electric spindle technology, applied in the field of workpiece grinding, can solve the problems of electric spindle burnout, large riser and flash, under-grinding, etc., so as to avoid impact collision and protect the electric spindle from burning out.
- Summary
- Abstract
- Description
- Claims
- Application Information
AI Technical Summary
Problems solved by technology
Method used
Image
Examples
Embodiment Construction
[0023] The present invention will be further described below in conjunction with the accompanying drawings and specific embodiments.
[0024] A floating spindle, see Figures 1 to 7 , including an electric spindle 12, the top of the electric spindle 12 is fixed with a grinding tool 1 through a tool handle 11, and one end of the electric spindle 12 fixed with the grinding tool 1 is provided with a protective sleeve, from the top of the electric spindle 12 to the end The direction of the end is coaxial with the electric main shaft 12 in turn, and the first protective sleeve 2, the end cover 29, the rotating frame 13, the second piston ring 14, the transition plate 19, the pressure ring 30, the expansion inner ring 20, the expansion outer ring Ring 21, first piston ring 22, displacement sensor 24, housing sealing plate 26, first flange 25 and second protective sleeve 23.
[0025] Specifically, the electric spindle 12 passes through a first piston ring 22, a displacement sensor 2...
PUM
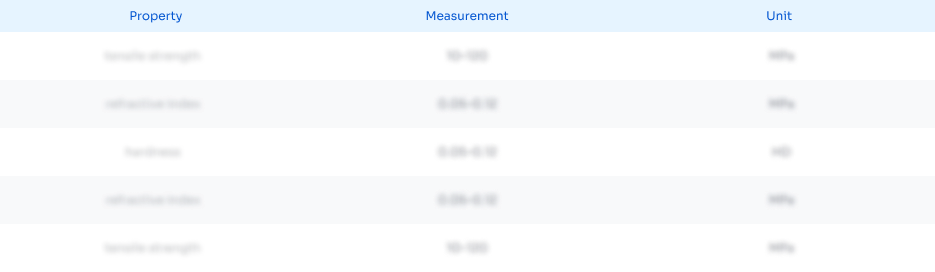
Abstract
Description
Claims
Application Information

- Generate Ideas
- Intellectual Property
- Life Sciences
- Materials
- Tech Scout
- Unparalleled Data Quality
- Higher Quality Content
- 60% Fewer Hallucinations
Browse by: Latest US Patents, China's latest patents, Technical Efficacy Thesaurus, Application Domain, Technology Topic, Popular Technical Reports.
© 2025 PatSnap. All rights reserved.Legal|Privacy policy|Modern Slavery Act Transparency Statement|Sitemap|About US| Contact US: help@patsnap.com