Cotter spring pin curling production method and equipment thereof
A technology of production equipment and production methods, applied in the direction of mechanical equipment, pins, connecting components, etc., can solve problems such as low production efficiency and slow work rhythm, and achieve the effect of improving processing efficiency and ensuring consistency
- Summary
- Abstract
- Description
- Claims
- Application Information
AI Technical Summary
Problems solved by technology
Method used
Image
Examples
Embodiment Construction
[0023] like figure 2 As shown, a cotter pin crimping production equipment, the equipment includes a base plate and a driving device 1 installed on the base plate, a feeding device 2, a positioning forming device 3 and a crimping device 4. The drive device 1 comprises a drive shaft 11 . The driving shaft 11 is arranged horizontally and rotates in a circumferential direction. The output end of the driving shaft 11 is connected to the positioning forming device 3 and drives the positioning forming device 3 to rotate around the driving shaft 11 . There are at least three crimping devices 4 . The crimping device 4 is distributed along the circumferential direction of the positioning forming device 3 , the positioning forming device 3 drives the crimping device 4 to rotate through the gear assembly 5 , and the positioning forming device 3 and the crimping device 4 rotate in opposite directions. The feeding device 2 is driven to be positioned at the side of the positioning forming...
PUM
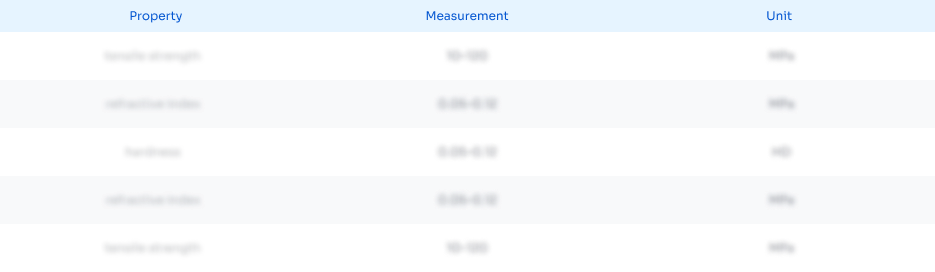
Abstract
Description
Claims
Application Information

- R&D
- Intellectual Property
- Life Sciences
- Materials
- Tech Scout
- Unparalleled Data Quality
- Higher Quality Content
- 60% Fewer Hallucinations
Browse by: Latest US Patents, China's latest patents, Technical Efficacy Thesaurus, Application Domain, Technology Topic, Popular Technical Reports.
© 2025 PatSnap. All rights reserved.Legal|Privacy policy|Modern Slavery Act Transparency Statement|Sitemap|About US| Contact US: help@patsnap.com