Spiral core-pulling mold for transmission sleeve
A transmission sleeve and spiral technology, applied in the field of spiral core-pulling molds, can solve the problems of slow cooling speed, slow forming, and poor precision, and achieve the effects of high precision, easy rotation, and guaranteed size
- Summary
- Abstract
- Description
- Claims
- Application Information
AI Technical Summary
Problems solved by technology
Method used
Image
Examples
Embodiment 1
[0046] A spiral core-pulling die for transmission sleeves, such as figure 1 It is a schematic diagram of the structural relationship of the transmission sleeve in the prior art, such as Figure 2-9 Shown is a schematic diagram of the mold structure relationship, including an upper mold assembly 1 and a lower mold assembly 2, four stations are arranged between the upper mold assembly 1 and the lower mold assembly 2, and the upper mold assembly 1 is from top to bottom The upper top plate 11, the feeding plate 12 and the movable platen 13 are arranged in sequence, the lower mold assembly 2 includes a fixed platen 21 arranged on the top, and four upper mold cores 3 are arranged on the movable platen 13, and the inner part of the feeding plate 12 A feed pipeline is provided, and the upper mold core 3 is provided with a feed passage 31 connected to the feed pipeline. The fixed template 21 is correspondingly provided with a lower mold core 22 and a lower mold insert 23. The upper mol...
Embodiment 2
[0058] A threaded core-pulling die for transmission sleeves, such as Figure 10 As shown, the difference between this embodiment and the above-mentioned embodiments is that a water baffle 55 is arranged in the cooling water channel 42, and the water baffle 55 separates the water inlet 44 and the water outlet 45, and when the water flows through the water inlet 44 into the cooling When inside the water channel 42, under the action of the baffle plate 55, the water flow can flow up to the top and then flow down to form an inverted U-shaped water path, so as to ensure sufficient cooling effect and avoid the straight flow of water flow to a certain extent straight out.
PUM
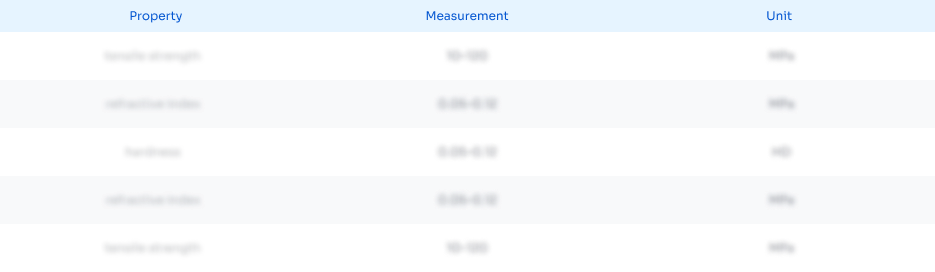
Abstract
Description
Claims
Application Information

- R&D
- Intellectual Property
- Life Sciences
- Materials
- Tech Scout
- Unparalleled Data Quality
- Higher Quality Content
- 60% Fewer Hallucinations
Browse by: Latest US Patents, China's latest patents, Technical Efficacy Thesaurus, Application Domain, Technology Topic, Popular Technical Reports.
© 2025 PatSnap. All rights reserved.Legal|Privacy policy|Modern Slavery Act Transparency Statement|Sitemap|About US| Contact US: help@patsnap.com