On-Line Compensation Method and System for Phase Delay of Micromachined Gyro Interface Circuit
A micromachined gyroscope and interface circuit technology, which is applied in the direction of gyroscopic effect for speed measurement, gyroscope/steering sensing equipment, instruments, etc., can solve the problems of micromachined gyroscope measurement drift and instability, and achieve automatic compensation and normal measurement. Effect
- Summary
- Abstract
- Description
- Claims
- Application Information
AI Technical Summary
Problems solved by technology
Method used
Image
Examples
Embodiment Construction
[0030] The present invention will be further described in detail below with reference to the accompanying drawings.
[0031] like figure 1 As shown, an online real-time automatic compensation method for the phase delay of the modal interface circuit of the micromachined gyroscope is used to detect the movement of the modalities of the micromachined gyroscope under the action of the Coriolis angular velocity force, the in-phase bias and the orthogonal error force. After the signal is converted into a voltage signal, the original measurement output value and the synchronous auxiliary output value are obtained respectively after the original measurement module and the synchronous auxiliary module. After the combined operation, the original measurement output value and the synchronous auxiliary output value can be automatically obtained in real time. The residual fluctuation value of the phase delay of the circuit, the obtained residual fluctuation value of the phase delay of the in...
PUM
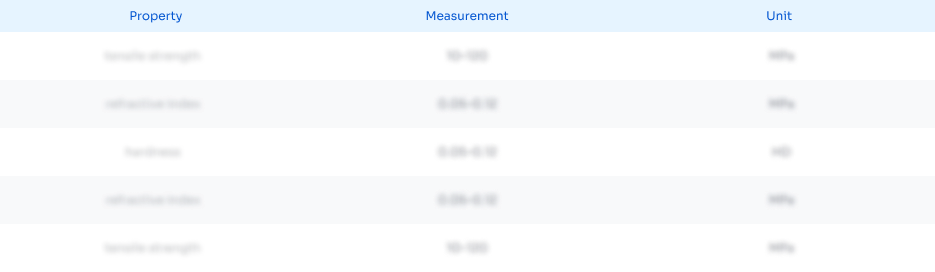
Abstract
Description
Claims
Application Information

- Generate Ideas
- Intellectual Property
- Life Sciences
- Materials
- Tech Scout
- Unparalleled Data Quality
- Higher Quality Content
- 60% Fewer Hallucinations
Browse by: Latest US Patents, China's latest patents, Technical Efficacy Thesaurus, Application Domain, Technology Topic, Popular Technical Reports.
© 2025 PatSnap. All rights reserved.Legal|Privacy policy|Modern Slavery Act Transparency Statement|Sitemap|About US| Contact US: help@patsnap.com