Automatic powder feeding tool for ceramic-lined pipe line
A ceramic lining and pipeline technology, which is applied in the field of automatic powder feeding equipment for ceramic lining pipes, can solve problems such as poor precision, powder dust pollution, and poor working environment for workers, and achieve convenient use and good results
- Summary
- Abstract
- Description
- Claims
- Application Information
AI Technical Summary
Problems solved by technology
Method used
Image
Examples
Embodiment 1
[0029] Embodiment 1: An automatic powder feeding tool for ceramic lined pipes, including symmetrically arranged strip-shaped left L-shaped sheet metal parts 1 and right L-shaped sheet metal parts 2, two long strip-shaped left The L-shaped sheet metal part 1 and the right L-shaped sheet metal part 2 can be set to be consistent with the length of the carbon steel pipe 100 to be coated, and the left L-shaped sheet metal part 1 and the right L-shaped sheet metal part 2 can be selected Similar to angle steel sheet metal parts, two L-shaped sheet metal parts are close to each other to form a groove-like structure, and a flat end surface is formed at the bottom for powder loading. The left L-shaped sheet metal part 1 and the right L-shaped L-shaped sheet metal part 2 can be separated, that is, the left L-shaped sheet metal part 1 and the right L-shaped When the joints of the L-shaped sheet metal parts 2 are separated from each other, the bottom can be opened to realize the function o...
Embodiment 2
[0034] The difference from Embodiment 1 of the present application is that, as shown in the description attached Figure 5-7 As shown, a connection spring 7 is fixedly connected between the two normally closed vise heads 51, and an electromagnet 8 is fixedly connected to one end of the two opening and closing vise heads 61 that are close to each other. The connection spring 7 in the stretched state is fixedly connected, and the two electromagnets 8 are energized to repel each other away from each other. As attached to the manual Figure 5 As shown, the connection spring 7 is in an extended state, and the connection spring 7 will provide a force to pull the normally closed vise head 51 inward, thereby pulling the normally closed vise handle 52 inward, and driving the sheet metal on the left and right sides The lower end of the part is squeezed inward, so that the gasket 3 at the bottom of the sheet metal part is squeezed by the reaction force, so that the bottoms of the two L-...
PUM
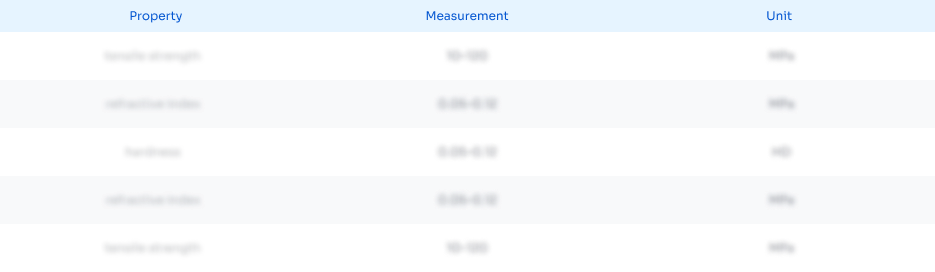
Abstract
Description
Claims
Application Information

- R&D
- Intellectual Property
- Life Sciences
- Materials
- Tech Scout
- Unparalleled Data Quality
- Higher Quality Content
- 60% Fewer Hallucinations
Browse by: Latest US Patents, China's latest patents, Technical Efficacy Thesaurus, Application Domain, Technology Topic, Popular Technical Reports.
© 2025 PatSnap. All rights reserved.Legal|Privacy policy|Modern Slavery Act Transparency Statement|Sitemap|About US| Contact US: help@patsnap.com