Method for reduction treatment on high-silicon slag through alkali-saving roasting method
A roasting method and reduction technology, which is applied in the field of alkali-saving roasting method to reduce the amount of high-silicon waste residue, can solve the problems of heavy material burden, shorten roasting time, and large amount of recycled alkali, and achieve material burden Lightweight, easy to obtain, and less residue
- Summary
- Abstract
- Description
- Claims
- Application Information
AI Technical Summary
Problems solved by technology
Method used
Image
Examples
Embodiment 1
[0028] Use industrial caustic soda as alkali flux, weigh the alkali flux and high-silicon waste slag according to the mass ratio of industrial caustic soda to high-silicon waste slag as 1.4, 1.2, 1.8, 1.6, 1.7, 1.5, 2.0, and put them into the pre- In the mixer, pre-mix for 60s to make pre-mixed ore;
[0029] The mass fraction of silicon dioxide in the high-silicon waste residue is 65%;
[0030] Roasting at 500°C for 20 minutes to obtain roasted ore;
[0031] According to the order of groups 1 to 7, the premixed ore roasting temperature is controlled to 400°C, 300°C, 350°C, 500°C, 450°C, 600°C, 550°C respectively;
[0032] According to the order of groups 1 to 7, the premixed ore roasting time is controlled to 20, 10, 18, 33, 35, 24, 42 minutes;
[0033] After the roasting is completed, the roasted ore is added to 80°C hot water for leaching (the weight ratio of water and mineral is 5:1), and the obtained clear liquid and filter cake are filtered;
[0034] According to the o...
Embodiment 2
[0037] Use industrial caustic soda as alkali flux, weigh the alkali flux and high-silicon waste slag according to the mass ratio of industrial caustic soda to high-silicon waste slag as 1.2, 1.8, 1.4, 1.6, 1.5, 1.7, 2.0, and put them into the pre- In the mixer, pre-mix for 60s to make pre-mixed ore;
[0038] The mass fraction of silicon dioxide in the high-silicon waste residue is 70%;
[0039] Roasting at 500°C for 20 minutes to obtain roasted ore;
[0040] According to the order of groups 1 to 7, the premixed ore roasting temperature is controlled to 300°C, 400°C, 350°C, 450°C, 500°C, 600°C, 550°C respectively;
[0041] According to the order of groups 1 to 7, the premixed ore roasting time is controlled to 10, 20, 18, 24, 33, 35, 42 minutes;
[0042] After the roasting is completed, the roasted ore is added to 80°C hot water for leaching (the weight ratio of water and mineral is 5:1), and the obtained clear liquid and filter cake are filtered;
[0043] In the order of gr...
Embodiment 3
[0046] Use industrial caustic soda as alkali flux, weigh the alkali flux and high-silicon waste slag according to the mass ratio of industrial caustic soda to high-silicon waste slag at 1.8, 1.4, 1.5, 1.6, 1.7, 2.0, 1.2, and put them into pre- In the mixer, pre-mix for 60s to make pre-mixed ore;
[0047] The mass fraction of silicon dioxide in the high-silicon waste residue is 74%;
[0048] Roasting at 500°C for 20 minutes to obtain roasted ore;
[0049] According to the order of groups 1 to 7, the roasting temperature of the premixed ore is controlled to 450°C, 400°C, 350°C, 550°C, 300°C, 600°C, 500°C respectively;
[0050] According to the order of groups 1 to 7, the premixed ore roasting time is controlled to 35, 20, 18, 25, 13, 30, 45 minutes;
[0051]After the roasting is completed, the roasted ore is added to 80°C hot water for leaching (the weight ratio of water and mineral is 5:1), and the obtained clear liquid and filter cake are filtered;
[0052] In the order of ...
PUM
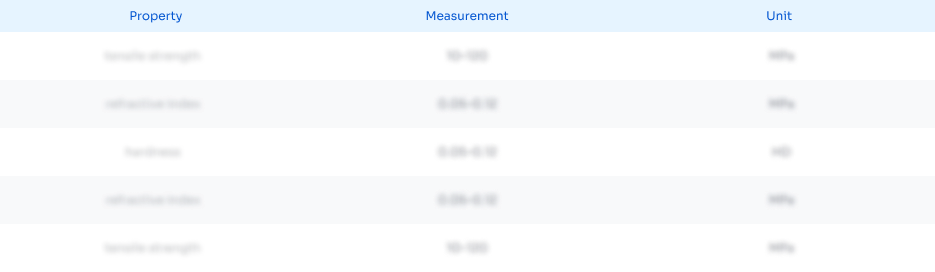
Abstract
Description
Claims
Application Information

- R&D Engineer
- R&D Manager
- IP Professional
- Industry Leading Data Capabilities
- Powerful AI technology
- Patent DNA Extraction
Browse by: Latest US Patents, China's latest patents, Technical Efficacy Thesaurus, Application Domain, Technology Topic, Popular Technical Reports.
© 2024 PatSnap. All rights reserved.Legal|Privacy policy|Modern Slavery Act Transparency Statement|Sitemap|About US| Contact US: help@patsnap.com