Non-woven fabric embossing process
A molding process and non-woven fabric technology, which is applied in high-pressure cleaning, textile and papermaking, fabric surface trimming, etc., and can solve problems such as embossing failure, non-woven fabric embossing barrier, non-woven fabric embossing forming incomplete, etc. , to achieve the effect of avoiding quality reduction and good stability
- Summary
- Abstract
- Description
- Claims
- Application Information
AI Technical Summary
Problems solved by technology
Method used
Image
Examples
Embodiment Construction
[0042] The following will clearly and completely describe the technical solutions in the embodiments of the present invention with reference to the accompanying drawings in the embodiments of the present invention. Obviously, the described embodiments are only some of the embodiments of the present invention, not all of them. Based on the embodiments of the present invention, all other embodiments obtained by persons of ordinary skill in the art without creative efforts fall within the protection scope of the present invention.
[0043] see Figure 1-13 , the present invention provides a technical solution: a non-woven fabric embossing forming process, including a bottom plate 1, a first mounting plate 2 is fixedly connected to the left side of the top of the bottom plate 1, and a shelf is fixedly connected to the front of the right wall of the first mounting plate 2. Roller 3, the rear part of the right side wall of the first installation plate 2 is rotatably connected with t...
PUM
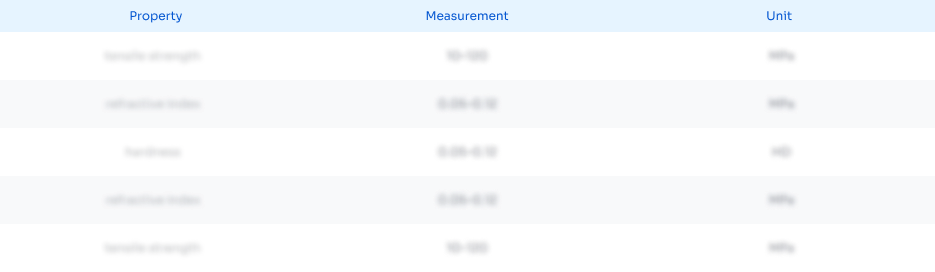
Abstract
Description
Claims
Application Information

- R&D
- Intellectual Property
- Life Sciences
- Materials
- Tech Scout
- Unparalleled Data Quality
- Higher Quality Content
- 60% Fewer Hallucinations
Browse by: Latest US Patents, China's latest patents, Technical Efficacy Thesaurus, Application Domain, Technology Topic, Popular Technical Reports.
© 2025 PatSnap. All rights reserved.Legal|Privacy policy|Modern Slavery Act Transparency Statement|Sitemap|About US| Contact US: help@patsnap.com