Edge cutting device and edge cutting method for thin-wall deep-drawn cylindrical part
A technology for deep cylindrical parts and cylindrical parts is applied in the field of trimming devices for thin-walled deep drawing cylindrical parts, which can solve the problems of complex device structure, poor trimming quality, processing deformation, etc. The effect of cutting edges without burrs
- Summary
- Abstract
- Description
- Claims
- Application Information
AI Technical Summary
Problems solved by technology
Method used
Image
Examples
Embodiment Construction
[0022] The specific implementation manners of the present invention will be further described in detail below in conjunction with the accompanying drawings.
[0023] A trimming device for a thin-walled cylindrical piece, comprising an upper mold base and a lower mold base, a cylindrical piece trimming mechanism is arranged between the upper mold base and the lower mold base, and the cylindrical piece trims The side mechanism includes a die 1, a core-fixing punch 2, a punching connecting sleeve 3 and a cylindrical knife 4, and the core-fixing punch 2 and the punching connecting sleeve 3 are arranged above the die 1, and the die 1, The axes of the centering punch 2 and the blanking connecting sleeve 3 are located on the same vertical line, the lower end of the die 1 is fixedly connected with the lower die base, and the upper end of the inner hole of the die 1 extends upwards and outwards to form a chamfer The supporting surface 5, the upper end of the fixed core punch 2 is fixed...
PUM
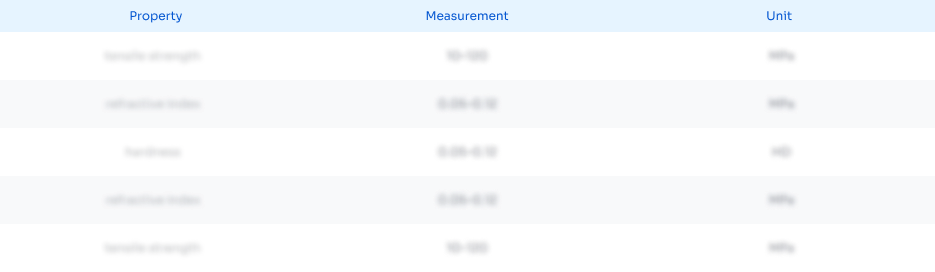
Abstract
Description
Claims
Application Information

- Generate Ideas
- Intellectual Property
- Life Sciences
- Materials
- Tech Scout
- Unparalleled Data Quality
- Higher Quality Content
- 60% Fewer Hallucinations
Browse by: Latest US Patents, China's latest patents, Technical Efficacy Thesaurus, Application Domain, Technology Topic, Popular Technical Reports.
© 2025 PatSnap. All rights reserved.Legal|Privacy policy|Modern Slavery Act Transparency Statement|Sitemap|About US| Contact US: help@patsnap.com