Main loop arrangement structure of three-phase alternating-current motor driving system controller
A motor drive system, three-phase AC technology, applied in the direction of AC motor control, control system, output power conversion device, etc., can solve problems such as reducing the reliability of motor drive control and affecting the switching characteristics of power modules
- Summary
- Abstract
- Description
- Claims
- Application Information
AI Technical Summary
Problems solved by technology
Method used
Image
Examples
Embodiment Construction
[0026] Example image 3 As shown, the main circuit layout structure of the three-phase AC motor drive system controller of the present invention includes a power module 1 with positive and negative busbars and a support capacitor 2 with positive and negative busbars, wherein the positive busbar 11 of the power module 1 The positive busbar 21 of the supporting capacitor 2 and the negative busbar 12 of the power module 1 and the negative busbar 22 of the supporting capacitor 2 are respectively connected with bolts 3 and inserts 4 to form an inverter main circuit. The positive and negative busbars of the power module 1 The busbars 11 and 12 extend along the installation plane to the position of the bolt 3 and the insert 4, the positive and negative busbars 21 and 22 of the support capacitor 2 extend horizontally in the direction of the power module 1 and then bend vertically to the positive and negative busbars. and then extend to the position of the bolt 3 and the insert 4 along...
PUM
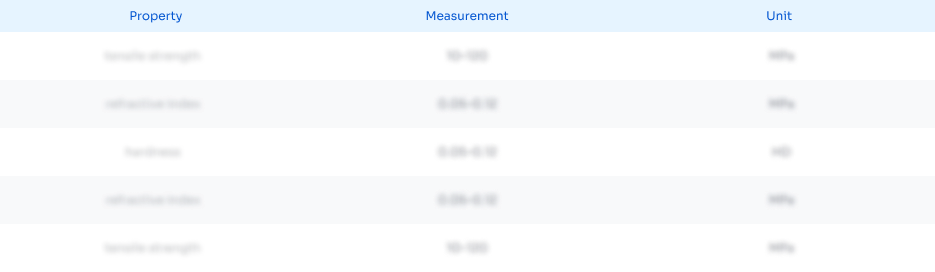
Abstract
Description
Claims
Application Information

- R&D Engineer
- R&D Manager
- IP Professional
- Industry Leading Data Capabilities
- Powerful AI technology
- Patent DNA Extraction
Browse by: Latest US Patents, China's latest patents, Technical Efficacy Thesaurus, Application Domain, Technology Topic, Popular Technical Reports.
© 2024 PatSnap. All rights reserved.Legal|Privacy policy|Modern Slavery Act Transparency Statement|Sitemap|About US| Contact US: help@patsnap.com