Method for welding non-melt-through insulating layer on outer-ring copper foil of transformer
A transformer and insulating layer technology, applied in the manufacture of inductors/transformers/magnets, preventing/reducing unwanted electric/magnetic influences, electrical components, etc., can solve the contact short circuit, detection, and melting insulation of the outer layer copper foil layers and other issues to achieve the effect of solving headaches
- Summary
- Abstract
- Description
- Claims
- Application Information
AI Technical Summary
Problems solved by technology
Method used
Image
Examples
Embodiment 1
[0020] In this embodiment, there is no need for deliberate and too precise control during welding, so even if there is a slight melting loss of the insulating adhesive layer (which can be insulating tape or any insulating material) caused by welding, the outer copper foil will never contact The short-circuit phenomenon of close contact with the inner wire wrap winding; the welding method referred to is not limited to soldering iron plus tin, and various other welding methods (such as laser welding) are applicable.
[0021] see Figure 1-Figure 2 As shown, the method for welding the copper foil of the outer ring of the transformer without melting through the insulating layer, the method includes the following steps:
[0022] (1) Set the transformer to be processed, including the magnetic core and wire wrap winding;
[0023] (2) Wind the copper foil on the outermost layer of the magnetic core. When winding, move the joint of the copper foil to the side and leave it on the side ...
PUM
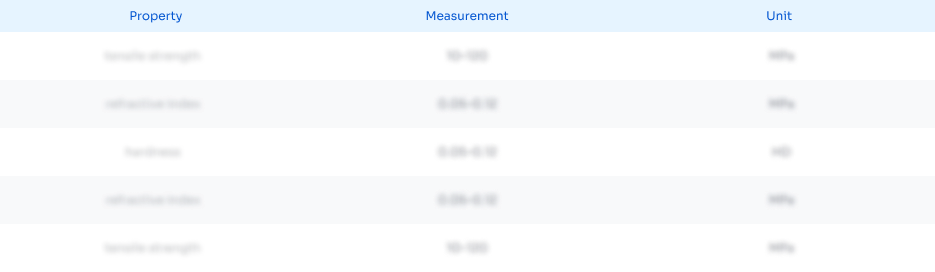
Abstract
Description
Claims
Application Information

- Generate Ideas
- Intellectual Property
- Life Sciences
- Materials
- Tech Scout
- Unparalleled Data Quality
- Higher Quality Content
- 60% Fewer Hallucinations
Browse by: Latest US Patents, China's latest patents, Technical Efficacy Thesaurus, Application Domain, Technology Topic, Popular Technical Reports.
© 2025 PatSnap. All rights reserved.Legal|Privacy policy|Modern Slavery Act Transparency Statement|Sitemap|About US| Contact US: help@patsnap.com