Planning method of ship hull plate curved surface forming collaborative machining based on dual mechanical arms
A technology of curved surface forming and dual manipulators, which is applied in the direction of manipulators, program control manipulators, manufacturing tools, etc., and can solve the problems of lack of analysis and task planning models, poor applicability, and consideration of constraints
- Summary
- Abstract
- Description
- Claims
- Application Information
AI Technical Summary
Problems solved by technology
Method used
Image
Examples
Embodiment Construction
[0057] The following will clearly and completely describe the technical solutions in the embodiments of the present invention with reference to the accompanying drawings in the embodiments of the present invention. Obviously, the described embodiments are only some, not all, embodiments of the present invention. Based on the embodiments of the present invention, all other embodiments obtained by persons of ordinary skill in the art without creative efforts fall within the protection scope of the present invention.
[0058] A planning method for collaborative machining of hull plate surface forming based on dual manipulators, combined with Figure 1 to Figure 6 As shown, it specifically includes the following steps:
[0059] S1. Modeling analysis. According to the requirement of co-machining process of hull shell surface forming and the extraction of heating path, the characteristics of heating path are obtained.
[0060] In step S1, the various characteristics of the heating...
PUM
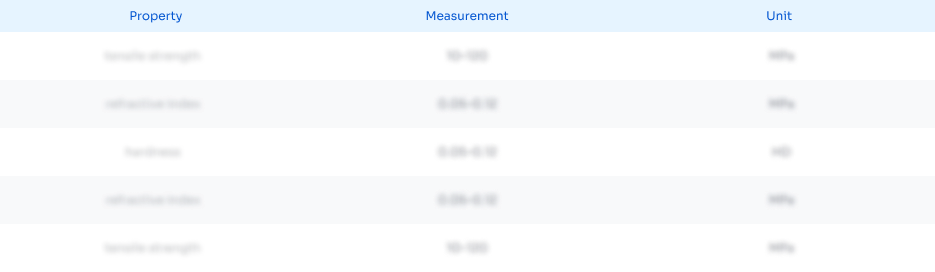
Abstract
Description
Claims
Application Information

- R&D Engineer
- R&D Manager
- IP Professional
- Industry Leading Data Capabilities
- Powerful AI technology
- Patent DNA Extraction
Browse by: Latest US Patents, China's latest patents, Technical Efficacy Thesaurus, Application Domain, Technology Topic, Popular Technical Reports.
© 2024 PatSnap. All rights reserved.Legal|Privacy policy|Modern Slavery Act Transparency Statement|Sitemap|About US| Contact US: help@patsnap.com